Distributed sensing system and method for simultaneously measuring fiber bragg grating vibration and strain
A fiber grating and sensing system technology, which is applied in the direction of using optical devices to transmit sensing components, measuring devices, and converting sensor outputs, etc., can solve problems such as low performance, high cost, and complex systems, and achieve vibration sensitivity and signal-to-noise ratio High, large measurement frequency range, good system compatibility
- Summary
- Abstract
- Description
- Claims
- Application Information
AI Technical Summary
Problems solved by technology
Method used
Image
Examples
Embodiment Construction
[0030] The present invention will be described in detail below in conjunction with the accompanying drawings, but the protection scope of the present invention should not be limited thereto.
[0031] Such as figure 1 As shown, the distributed sensing system for simultaneous measurement of fiber grating vibration and strain of the present invention includes a broadband spontaneous emission light source 1, a first fiber coupler 2, a time-delay fiber 3, a beam combiner 4, a second fiber coupler 5, A fiber grating sensor, a wavelength demodulation unit 7 , a data analysis and display unit 8 , a filter array 9 , a photodetector array 10 and a multi-channel data acquisition card 11 . Wherein the fiber grating sensor 6 includes gratings arranged at intervals along the length direction of the optical fiber, and in front of each grating is a transmission optical fiber of a certain length, see figure 2 As shown, the spaced gratings constitute a strain sensing array 6-1 for strain moni...
PUM
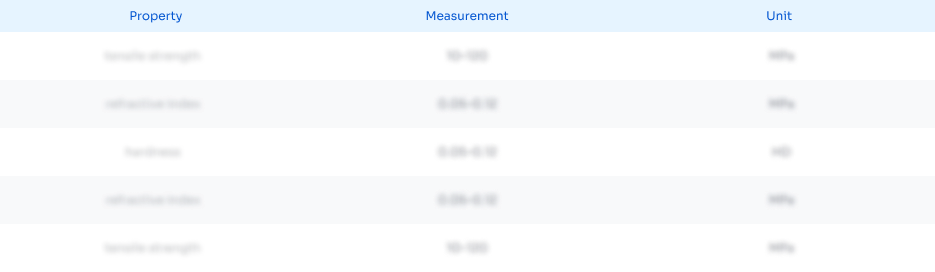
Abstract
Description
Claims
Application Information

- R&D
- Intellectual Property
- Life Sciences
- Materials
- Tech Scout
- Unparalleled Data Quality
- Higher Quality Content
- 60% Fewer Hallucinations
Browse by: Latest US Patents, China's latest patents, Technical Efficacy Thesaurus, Application Domain, Technology Topic, Popular Technical Reports.
© 2025 PatSnap. All rights reserved.Legal|Privacy policy|Modern Slavery Act Transparency Statement|Sitemap|About US| Contact US: help@patsnap.com