Preparation process of H08A steel
A preparation process and technology for molten steel, applied in the field of iron and steel metallurgy, can solve the problems of billet bubble defects, unoptimized addition method of deoxidizer, insignificant effect of bubbles and inclusions, etc., and achieve the effect of promoting effect.
- Summary
- Abstract
- Description
- Claims
- Application Information
AI Technical Summary
Problems solved by technology
Method used
Image
Examples
Embodiment 1
[0042] 1) Converter smelting: pre-treat the molten steel used in large-tonnage (100T) converter smelting, control C0.04% and P0.06% in molten steel, and control S0.03% through converter top-bottom combined blowing, and control converter tapping The temperature is 1590 ° C. During the tapping process, the powdered Mg-Ca alloy with a mass fraction of 0.34% is blown into the bottom of the ladle for pre-deoxidation by using an inert gas through the conduit connected to the bottom of the ladle. The blowing rate is controlled at 0.25kg / s, the stirring time is 10min with the argon blowing into the inlet, and the free oxygen content of the molten steel is controlled at 100ppm;
[0043] 2) LF refining: during the refining process, the calcium wire is quickly injected into the molten steel to remove oxygen again. The injection speed of the calcium wire is 230m / min, and the injected content is 0.05wt%. Stirring; control the free oxygen content of molten steel LF refining and heating to ...
Embodiment 2
[0046] 1) Converter smelting: Pretreatment of molten steel used in large-tonnage (100T) converter smelting, controlling C0.04% and P0.05% in molten steel, controlling S0.03% through converter top-bottom composite blowing, and controlling converter tapping The temperature is 1550 ° C. During the tapping process, the powdered Mg-Si alloy with a mass fraction of 0.42% is blown into the bottom of the ladle for pre-deoxidation by using an inert gas through the conduit connected to the bottom of the ladle. The blowing rate is controlled at 0.43kg / s, the stirring time is 10min with the argon blowing into the inlet, and the free oxygen content of the molten steel is controlled at 90ppm;
[0047] 2) LF refining: During the refining process, the calcium wire is quickly injected into the molten steel to remove oxygen again. The injection speed of the calcium wire is 250m / min, and the injected content is 0.06wt%. Stirring; control the free oxygen content of molten steel LF refining and h...
Embodiment 3
[0050] 1) Converter smelting: pre-treat the molten steel used in large-tonnage (100T) converter smelting, control the C in the molten steel to 0.05%, P 0.04%, and control the S 0.03% through the top-bottom compound blowing of the converter, and control the tapping of the converter The temperature is 1550 ° C. During the tapping process, the powdered Mg-Sr alloy with a mass fraction of 0.19% is blown into the bottom of the ladle for pre-deoxidation by using an inert gas through the conduit connected to the bottom of the ladle. The blowing rate is controlled at 0.14kg / s, stirring with argon blowing for 7 minutes, and controlling the free oxygen content of molten steel at 90ppm;
[0051] 2) LF refining: during the refining process, the calcium wire is quickly injected into the molten steel to remove oxygen again. The injection speed of the calcium wire is 270m / min, and the injected content is 0.02wt%. Stirring; control the free oxygen content of molten steel LF refining and heat...
PUM
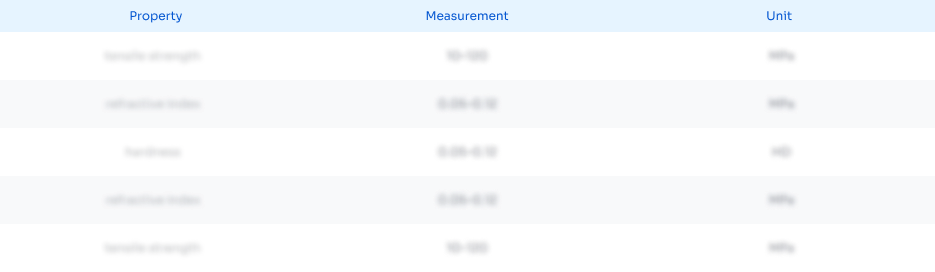
Abstract
Description
Claims
Application Information

- R&D
- Intellectual Property
- Life Sciences
- Materials
- Tech Scout
- Unparalleled Data Quality
- Higher Quality Content
- 60% Fewer Hallucinations
Browse by: Latest US Patents, China's latest patents, Technical Efficacy Thesaurus, Application Domain, Technology Topic, Popular Technical Reports.
© 2025 PatSnap. All rights reserved.Legal|Privacy policy|Modern Slavery Act Transparency Statement|Sitemap|About US| Contact US: help@patsnap.com