Ultralow-load stable-combustion pre-pyrolysis combustion system and ultralow-load operation method
A combustion system and pre-pyrolysis technology, applied in the field of boiler combustion, can solve the problems of high nitrogen oxide emissions, unsteady operation of once-through burners, and easy slagging, etc., to reduce NOx emissions, suppress the formation of NOx, and more benefit effect
- Summary
- Abstract
- Description
- Claims
- Application Information
AI Technical Summary
Problems solved by technology
Method used
Image
Examples
Embodiment 1
[0047] Embodiment 1, when a 600MW boiler is operating under full load conditions, five coal mills 1 are in operation, and one coal mill 1 is in standby. Each coal mill 1 sends primary air powder to the direct-flow burner 4 in the corresponding burner layer through the first powder feeding pipeline 3, and the auxiliary air is provided by the bellows 2, and the primary air powder and auxiliary air are mixed and injected into the boiler furnace 8 In the interior, it is directly impacted by the high-temperature flame sweeping from the upstream adjacent corner, and the ignition conditions are superior, and the fire can be stably ignited. For layer C of the main burner 12, under full load conditions, its four preheating and deswirling flow burners 7 are temporarily not in operation, and only four direct flow burners 4 are in operation. The A channel and the C channel of the reversing valve 5 of the powder feeding pipeline are opened, the B channel is closed, and the secondary air re...
Embodiment 2
[0048] Embodiment 2, when the 600MW boiler is operating under 80% load condition, the burner in layer A is turned off and the corresponding coal mill 1 is deactivated, and the other four coal mills 1 are operated, and one coal mill 1 is in standby. At this time, the conveying mode of the primary air powder and auxiliary air of the boiler is exactly the same as that of the first embodiment. Each coal mill 1 sends primary air powder to the direct-flow burner 4 in the corresponding burner layer through the first powder feeding pipeline 3, and the auxiliary air is provided by the bellows 2, and the primary air powder and auxiliary air are mixed and injected into the boiler furnace 8 inside, then a steady fire. Four preheating deswirling flow burners 7 are not in operation temporarily, and only four direct current burners 4 are operated. The A channel and C channel of the reversing valve 1 of the powder feeding pipeline are opened, the B channel is closed, and the secondary air re...
Embodiment 3
[0049] Example 3: When a 600MW boiler is operating at 60% load, turn off the A-layer and B-layer burners and deactivate the corresponding coal mill 1, run the other three coal mills 1, and one coal mill 1 for standby . At this time, the conveying mode of the primary air powder and the auxiliary air of the boiler is exactly the same as that of Embodiment 1, so it will not be described again.
PUM
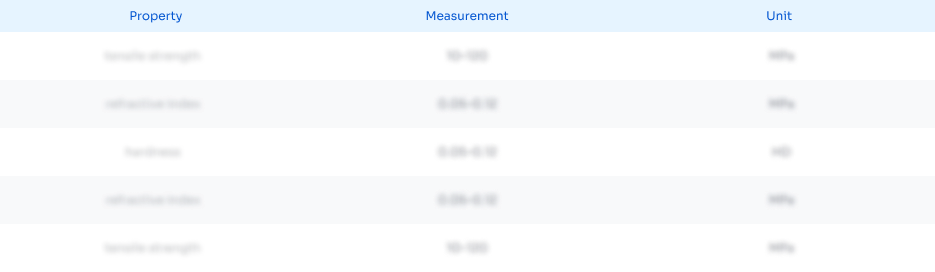
Abstract
Description
Claims
Application Information

- R&D
- Intellectual Property
- Life Sciences
- Materials
- Tech Scout
- Unparalleled Data Quality
- Higher Quality Content
- 60% Fewer Hallucinations
Browse by: Latest US Patents, China's latest patents, Technical Efficacy Thesaurus, Application Domain, Technology Topic, Popular Technical Reports.
© 2025 PatSnap. All rights reserved.Legal|Privacy policy|Modern Slavery Act Transparency Statement|Sitemap|About US| Contact US: help@patsnap.com