Method for preparing high-dispersity high-concentration monochromatic master batch and application of high-dispersity high-concentration monochromatic master batch
A high-dispersion, high-concentration technology, which is applied in the method of high-dispersion and high-concentration single-color masterbatch and its application field, can solve the problems of color difference, color point, and the influence of product appearance on the coloring, and achieve the reduction of dispersion, The effect of blemish improvement
- Summary
- Abstract
- Description
- Claims
- Application Information
AI Technical Summary
Problems solved by technology
Method used
Examples
Embodiment 1
[0034] Step one, heavy. Weigh 40% of carrier resin, 30% of colorant, 5% of compatibilizer, 5% of light stabilizer and 10% of calcium carbonate according to the mass percentage ratio of the raw materials.
[0035] Step 2, stereotypes. Add the heavy finished material in step 1 to the high-low speed mixer, the mixing time is 10-30min, and mix until the raw material forms a lump;
[0036] Step 3, adding auxiliary materials. Stop the mixer, add sodium methylene bis-naphthalene sulfonate with a mass percentage ratio of 10% of raw materials into the mixer, start the mixer again, and mix for 2 to 5 minutes.
[0037] Step four, grinding. The mixed raw materials are taken out from the mixer, and added to a three-roll mill for grinding until uniformly dispersed;
[0038] Step five, making. Put the ground raw materials into a single-screw extruder to extrude and pelletize. The particle size of the masterbatch should be greater than 3mm.
[0039] Step six, drying and finalizing. Put...
Embodiment 2
[0042] Step one, heavy. Weigh 40% of carrier resin, 30% of colorant, 5% of compatibilizer, 5% of light stabilizer and 10% of calcium carbonate according to the mass percentage ratio of the raw materials.
[0043] Step 2, stereotypes. Add the heavy finished material in step 1 to the high-low speed mixer, the mixing time is 10-30min, and mix until the raw material forms a lump;
[0044] Step 3, adding auxiliary materials. Stop the mixer, add sodium methylene bis-naphthalene sulfonate with a mass percentage ratio of 10% of raw materials into the mixer, start the mixer again, and mix for 2 to 5 minutes.
[0045] Step four, grinding. The mixed raw materials are taken out from the mixer, and added to a three-roll mill for grinding until uniformly dispersed;
[0046] Step five, making. Put the ground raw materials into a single-screw extruder to extrude and pelletize.
[0047] Step six, drying and finalizing. Put the masterbatch into the dryer for drying, and the drying time s...
Embodiment 3
[0050] Step one, heavy. Weigh 40% of carrier resin, 30% of colorant, 5% of compatibilizer, 5% of light stabilizer and 10% of calcium carbonate according to the mass percentage ratio of the raw materials.
[0051] Step 2, stereotypes. Add the heavy finished material in step 1 to the high-low speed mixer, the mixing time is 10-30min, and mix until the raw material forms a lump;
[0052] Step 3, adding auxiliary materials. Stop the mixer, add sodium methylene bis-naphthalene sulfonate with a mass percentage ratio of 10% of raw materials into the mixer, start the mixer again, and mix for 2 to 5 minutes.
[0053] Step four, grinding. The mixed raw materials are taken out from the mixer, and added to a three-roll mill for grinding until uniformly dispersed;
[0054]Step five, making. Put the ground raw materials into a single-screw extruder to extrude and pelletize, and the particle size of the masterbatch is 6mm.
[0055] Step six, drying and finalizing. Put the masterbatch ...
PUM
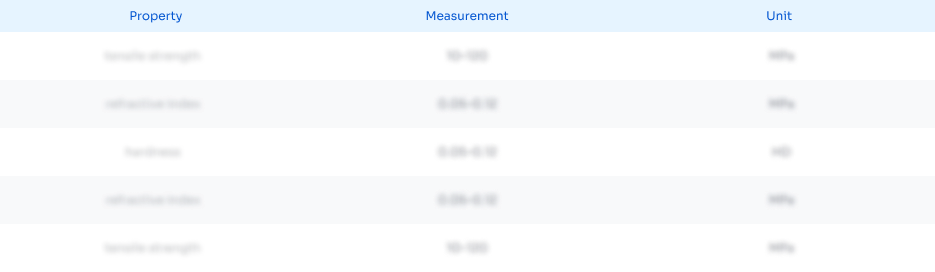
Abstract
Description
Claims
Application Information

- R&D Engineer
- R&D Manager
- IP Professional
- Industry Leading Data Capabilities
- Powerful AI technology
- Patent DNA Extraction
Browse by: Latest US Patents, China's latest patents, Technical Efficacy Thesaurus, Application Domain, Technology Topic, Popular Technical Reports.
© 2024 PatSnap. All rights reserved.Legal|Privacy policy|Modern Slavery Act Transparency Statement|Sitemap|About US| Contact US: help@patsnap.com