Preparation method and application of NiFe-LDH composite material
A composite material, ni-bdc technology, applied in electrodes, electrolysis process, electrolysis components, etc., can solve problems such as high cost and development constraints
- Summary
- Abstract
- Description
- Claims
- Application Information
AI Technical Summary
Problems solved by technology
Method used
Image
Examples
Embodiment 1
[0026] (1) Add BDC (0.75 mmol) to a mixture of 32 mL DMF, 2 mL ethanol and 2 mL water, ultrasonically disperse for 1 h, and then add 90 mg NiCl 2 ·6H 2 O. NiCl 2 ·6H 2 After O was completely dissolved, 0.8 mL of TEA was quickly added to the above solution. Then the solution was magnetically stirred for 1 h, and then ultrasonically continued for 8 h. Finally, the final product was collected by centrifugation, washed repeatedly with ethanol and DMF, and dried at 60°C for 5 hours to obtain the Ni-BDC precursor;
[0027] (2) Add Ni-BDC (20 mg) into 40 mL deionized water and sonicate for 2 h, then add iron nitrate Fe 2 (NO 3 ) 3 9H 2 O, (20 mg) and ammonium fluoride (NH 4 F, 1.48 mg) was slowly added to the above solution, and stirred to form a relatively dispersed suspension. NaOH (1 mol / L) and NCO 3 (1 mol / L) mixed at a volume ratio of 1:1 to obtain NaOH / NaCO 3 Buffer, NaOH / NaCO 3 Buffer was added dropwise to the suspension until pH=10. Finally, the solution was tra...
Embodiment 2
[0030] (1) Same as embodiment 1;
[0031] (2) Ni-BDC (20 mg) was sonicated in 40 mL deionized water for 2 h. Then iron nitrate Fe 2 (NO 3 )3 9H 2 O, (40mg) and ammonium fluoride (NH 4 F, 1.48 mg) was slowly added to the above solution, and stirred to form a relatively dispersed suspension. NaOH (1mol / L) and NCO 3 (1 mol / L) mixed at a volume ratio of 1:1 to obtain NaOH / NaCO 3 Buffer, NaOH / NaCO 3 Buffer was added dropwise to the suspension until pH=10. Finally, the solution was transferred to a 100 mL stainless steel autoclave lined with Teflon, heated at 140 °C for 12 h, and then allowed to stand to room temperature. The final solid product was collected by centrifugation and washed repeatedly with water and ethanol. Denote the product as NiFe-LDH-A2;
[0032] (3) Electrochemical performance test of NiFe-LDH-A2: at a current density of 10 mA / cm 2 , the overpotential of NiFe-LDH-A2 is 264 mV, Tafel is 57 mV dec -1 .
Embodiment 3
[0034] (1) Same as embodiment 1;
[0035] (2) Ni-BDC (20 mg) was sonicated in 40 mL deionized water for 2 h. Then ferric nitrate (Fe 2 (NO 3 ) 3 9H 2 O, 60mg) and ammonium fluoride (NH 4 F, 1.48 mg) was slowly added to the above solution, and stirred to form a relatively dispersed suspension. NaOH (1mol / L) and NCO 3 (1 mol / L) mixed at a volume ratio of 1:1 to obtain NaOH / NaCO 3 Buffer, NaOH / NaCO 3 Buffer was added dropwise to the suspension until pH=10. Finally, the solution was transferred to a 100 mL stainless steel autoclave lined with Teflon, heated at 140 °C for 12 h, and then allowed to stand to room temperature. The final solid product was collected by centrifugation and washed repeatedly with water and ethanol. Denote the product as NiFe-LDH-A3;
[0036] (3) Electrochemical performance test of NiFe-LDH-A3: at a current density of 10 mA / cm 2 , the overpotential of NiFe-LDH-A3 is 290 mV, Tafel is 55 mV dec -1 .
PUM
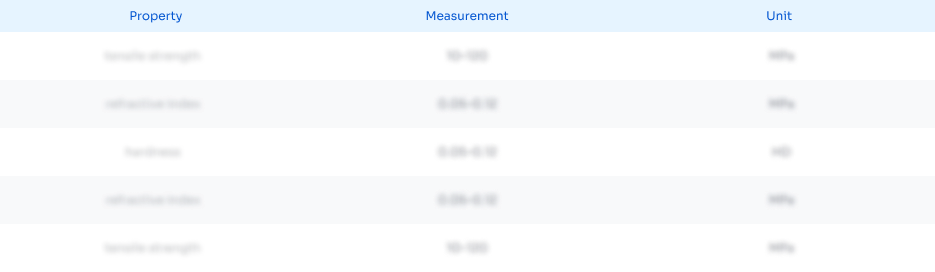
Abstract
Description
Claims
Application Information

- R&D Engineer
- R&D Manager
- IP Professional
- Industry Leading Data Capabilities
- Powerful AI technology
- Patent DNA Extraction
Browse by: Latest US Patents, China's latest patents, Technical Efficacy Thesaurus, Application Domain, Technology Topic, Popular Technical Reports.
© 2024 PatSnap. All rights reserved.Legal|Privacy policy|Modern Slavery Act Transparency Statement|Sitemap|About US| Contact US: help@patsnap.com