Novel textile steel wire ring molding machine tool
A traveler and textile technology, applied in the field of new textile traveler forming machine tools, can solve problems such as low processing efficiency and complex structure, achieve the effects of improving forming accuracy, improving equipment flexibility, and avoiding the reduction of forming accuracy
- Summary
- Abstract
- Description
- Claims
- Application Information
AI Technical Summary
Problems solved by technology
Method used
Image
Examples
Embodiment Construction
[0035] The present invention will be described in detail below in conjunction with the accompanying drawings and specific embodiments.
[0036] Such as figure 1 , the traveler forming machine tool of the present invention is sequentially provided with a feeding unit 1, a straightening unit 2, a window unit 3, a wire feeding unit 4, a forming unit 5 and a material returning unit according to the feeding route (because the returning unit is located in the forming unit 5 on the back, so the figure 1 The material return unit is not drawn in ); among them, the discharge unit 1 is driven by the discharge motor, which is a single-input single-output driving mode; the wire feeding unit 4 is driven by a wire-feeding motor, which is a single-input single-output driving mode; the window opening unit 3 , the molding unit 5 and the stripping unit are uniformly driven by the molding motor 6.2 (called an asynchronous motor), which is a single-input multi-output drive mode, see figure 2 . ...
PUM
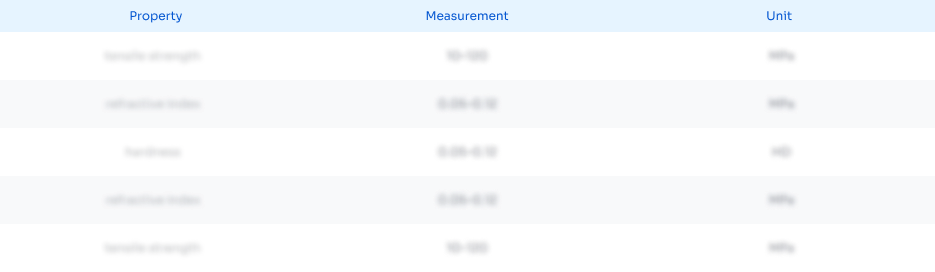
Abstract
Description
Claims
Application Information

- R&D
- Intellectual Property
- Life Sciences
- Materials
- Tech Scout
- Unparalleled Data Quality
- Higher Quality Content
- 60% Fewer Hallucinations
Browse by: Latest US Patents, China's latest patents, Technical Efficacy Thesaurus, Application Domain, Technology Topic, Popular Technical Reports.
© 2025 PatSnap. All rights reserved.Legal|Privacy policy|Modern Slavery Act Transparency Statement|Sitemap|About US| Contact US: help@patsnap.com