Steel for extremely-high forced wire and production method for controlling network cementite through hot-rolled wire rod of steel
A technology of hot-rolled wire rod and production method, applied in the direction of improving process efficiency, etc., to achieve the effect of reducing processing costs
- Summary
- Abstract
- Description
- Claims
- Application Information
AI Technical Summary
Problems solved by technology
Method used
Image
Examples
Embodiment 1
[0018] Example 1 is a hot-rolled steel wire rod for 100-grade extremely high-strength wire, chemical composition weight percentage: C: 0.99%, Si: 0.20%, Mn: 0.30%, Cr: 0.40%, V: 0.08%, residual iron and A small amount of residual impurity elements. The production process includes electric furnace smelting, LF furnace refining + VD, continuous casting bloom, two-fire billet rolling into wire rod. Specifically include the following steps:
[0019] (1) Electric furnace smelting: The electric furnace normally smelts and taps steel, and the tapping temperature is 1600°C. During the tapping process, rough alloying and carburization are carried out, and the remaining steel after tapping is 3 tons.
[0020] (2) LF furnace refining + VD: alloying and carburization are carried out during LF furnace refining, and the refining time is 58 minutes;
[0021] (3) Continuous casting; superheating degree 28°C, using 320mm×480mm bloom, controlling continuous casting casting speed 0.50m / min, ad...
Embodiment 2
[0024] Example 2 is a 97-grade extremely high-strength steel hot-rolled wire rod, chemical composition weight percentage: C: 0.95%, Si: 0.19%, Mn: 0.80%, Cr: 0.19%, residual iron and a small amount of residual impurity elements. Production process is consistent with embodiment 1, specifically comprises the following steps:
[0025] (1) Electric furnace smelting: The electric furnace normally smelts and taps steel, and the tapping temperature is 1590°C. During the tapping process, rough alloying and carburization are carried out, and the remaining steel after tapping is 4 tons.
[0026] (2) LF furnace refining + VD: Alloying and carburization are carried out during LF furnace refining, and the refining time is 56 minutes;
[0027] (3) Continuous casting; superheating degree 30°C, adopting 250mm×300mm bloom, controlling continuous casting casting speed 0.7m / min, adopting mold electromagnetic stirring 500A*4HZ, solidification end electromagnetic stirring 700A*6HZ and light reduct...
Embodiment 3
[0030] Example 3: It is a hot-rolled steel wire rod for 100-grade extremely high-strength wire, chemical composition weight percentage: C: 1.00%, Si: 0.19%, Mn: 0.28%, Cr: 0.38%, V: 0.09%, residual iron and a small amount of residual impurity elements. Production process is consistent with embodiment 1, specifically comprises the following steps:
[0031] (1) Electric furnace smelting: The electric furnace normally smelts and taps steel, and the tapping temperature is 1610°C. During the tapping process, rough alloying and carburization are carried out, and the remaining steel after tapping is 2.5 tons.
[0032] (2) LF furnace refining + VD: alloying and carburization are carried out during LF furnace refining, and the refining time is 55 minutes;
[0033] (3) Continuous casting; superheating degree 25°C, using 320mm×480mm bloom, controlling continuous casting casting speed 0.51m / min, adopting mold electromagnetic stirring 520A*2HZ, solidification end electromagnetic stirring ...
PUM
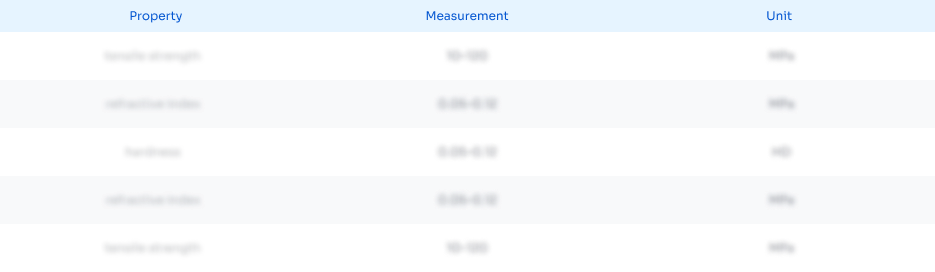
Abstract
Description
Claims
Application Information

- R&D
- Intellectual Property
- Life Sciences
- Materials
- Tech Scout
- Unparalleled Data Quality
- Higher Quality Content
- 60% Fewer Hallucinations
Browse by: Latest US Patents, China's latest patents, Technical Efficacy Thesaurus, Application Domain, Technology Topic, Popular Technical Reports.
© 2025 PatSnap. All rights reserved.Legal|Privacy policy|Modern Slavery Act Transparency Statement|Sitemap|About US| Contact US: help@patsnap.com