Piezoelectric two-dimensional fast reflecting mirror without axial displacement and driving and deflection angle measuring method
A technology of axial displacement and deflection angle, used in optical components, optics, instruments, etc., can solve the problems of short strain bridge signal lines, reduced control accuracy, increased measurement noise, etc., and achieves compact structure and simple driving form. , rich interface effects
- Summary
- Abstract
- Description
- Claims
- Application Information
AI Technical Summary
Problems solved by technology
Method used
Image
Examples
Embodiment Construction
[0031] Below in conjunction with accompanying drawing and specific embodiment, the present invention is described in further detail:
[0032] Such asfigure 1 with figure 2 As shown, a piezoelectric two-dimensional fast mirror without axial displacement of the present invention comprises a reflective mirror 1, a mirror holder 2 for installing the reflective mirror, a first displacement amplification mechanism 3, and a pressure plate with a strain gauge on the first surface. Electric stack 4, second displacement amplifying mechanism 6, second surface-mounted piezoelectric stack 5 of strain gauge, third displacement amplifying mechanism 9, third surface-mounted piezoelectric stack 10 of strain gauge, fourth displacement amplifying mechanism 12, the third Piezoelectric stack 11 with strain gauges on four surfaces, mounting base 7, and strain signal processing circuit 8;
[0033] The first displacement amplifying mechanism 3, the second displacement amplifying mechanism 6, the th...
PUM
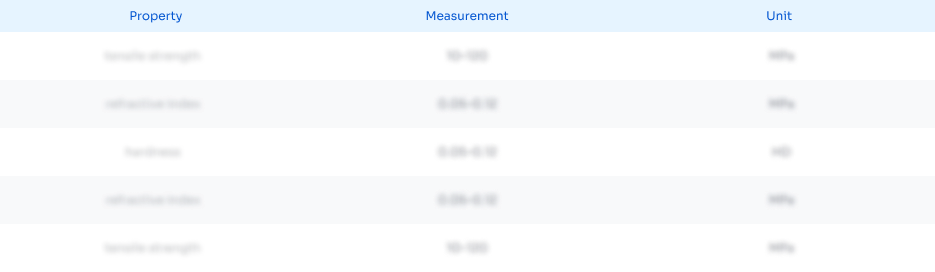
Abstract
Description
Claims
Application Information

- R&D Engineer
- R&D Manager
- IP Professional
- Industry Leading Data Capabilities
- Powerful AI technology
- Patent DNA Extraction
Browse by: Latest US Patents, China's latest patents, Technical Efficacy Thesaurus, Application Domain, Technology Topic, Popular Technical Reports.
© 2024 PatSnap. All rights reserved.Legal|Privacy policy|Modern Slavery Act Transparency Statement|Sitemap|About US| Contact US: help@patsnap.com