Production process of antibacterial regenerated polyester staple fibers
A technology of recycled polyester and production process, which is applied in fiber processing, filament forming processing, filament/thread forming, etc., can solve the problems of weak strength performance, limited market promotion, and difficulty in meeting the raw material strength from renewable resources, and achieves strength improvement. , Guarantee the efficiency, the effect of inhibiting the production of white powder
- Summary
- Abstract
- Description
- Claims
- Application Information
AI Technical Summary
Problems solved by technology
Method used
Image
Examples
Embodiment 1-3
[0055] Embodiment 1-3: This embodiment discloses an oil agent, which specifically includes the following components:
[0056] Polyoxyethylene fatty alcohol ether, potassium cetyl phosphate, cetyl benzyl dimethyl ammonium chloride, water.
[0057] In embodiment 1-3, the input amount (unit Kg) of each component sees table 2 for details
[0058] Table 2
[0059]
[0060] The preparation method of the oil agent is as follows: add polyoxyethylene fatty alcohol ether, potassium cetyl phosphate, and cetyl benzyl dimethyl ammonium chloride into a stirring tank equipped with water, stir while adding, and Under the condition of power of 900W and transmission frequency of 25kHz, the water bath ultrasonically oscillates for 2h.
Embodiment 4-6
[0061] Embodiment 4-6: This embodiment discloses a kind of oil agent, also adds following component:
[0062] Hexabromocyclododecane.
[0063] In embodiment 4-6, the input amount (unit Kg) of each component sees table 3 for details
[0064] table 3
[0065]
[0066] Add hexabromocyclododecane, polyoxyethylene fatty alcohol ether, potassium cetyl phosphate, and cetyl benzyl dimethyl ammonium chloride into a stirring tank filled with water.
Embodiment 7-9
[0067] Embodiment 7-9: This embodiment discloses a kind of oil preparation, also adds following component:
[0068] Hexabromocyclododecane, tricresyl phosphate.
[0069] In embodiment 7-9, the input amount (unit Kg) of each component sees table 4 for details
[0070] Table 4
[0071]
[0072]
[0073] Add hexabromocyclododecane, tricresyl phosphate, polyoxyethylene fatty alcohol ether, potassium cetyl phosphate, and cetyl benzyl dimethyl ammonium chloride into a stirring tank filled with water.
PUM
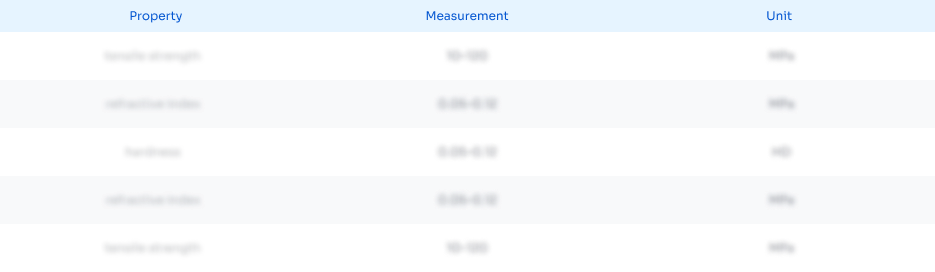
Abstract
Description
Claims
Application Information

- R&D
- Intellectual Property
- Life Sciences
- Materials
- Tech Scout
- Unparalleled Data Quality
- Higher Quality Content
- 60% Fewer Hallucinations
Browse by: Latest US Patents, China's latest patents, Technical Efficacy Thesaurus, Application Domain, Technology Topic, Popular Technical Reports.
© 2025 PatSnap. All rights reserved.Legal|Privacy policy|Modern Slavery Act Transparency Statement|Sitemap|About US| Contact US: help@patsnap.com