Novel electric furnace for producing high-purity sodium sulfide and process method
A sodium sulfide, electric furnace technology, applied in the direction of alkali metal sulfide/polysulfide, etc., can solve the problems of poor product stability, slow chemical rate, low heat utilization, etc., and achieve stable product quality, fast chemical rate and thermal efficiency. high effect
- Summary
- Abstract
- Description
- Claims
- Application Information
AI Technical Summary
Problems solved by technology
Method used
Image
Examples
Embodiment Construction
[0030] The present invention will be described in detail below in combination with specific embodiments.
[0031] like figure 1 As shown, a new electric furnace for producing high-purity sodium sulfide includes a steel structure of the furnace body 1, the steel structure of the furnace body includes a coaming, ribs, beams, springs, pull rods and nuts, and the coaming is made of refractory materials 2 The interior of the electric furnace is divided into two areas by the partition wall 3, namely the primary reduction smelting area 5 and the secondary clarification separation area 6; a hole 4 is reserved in the middle of the partition wall 3, so that the liquid sodium sulfide produced in the reduction smelting area 5 enters The secondary clarification and separation zone 6 is used for secondary clarification and separation; 6 graphite electrodes 7 are arranged inside the electric furnace to provide heat for the electric furnace; a flue 8 is provided on the top of the electric fur...
PUM
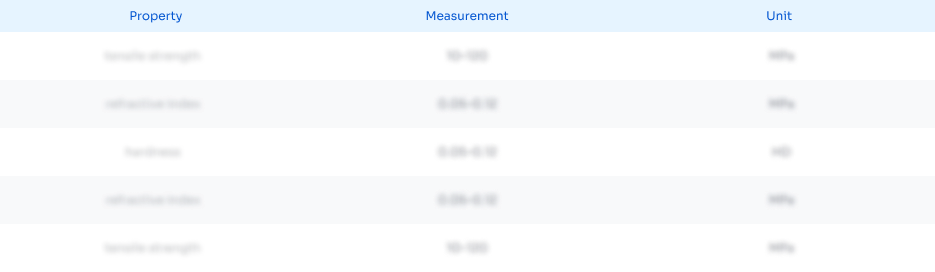
Abstract
Description
Claims
Application Information

- Generate Ideas
- Intellectual Property
- Life Sciences
- Materials
- Tech Scout
- Unparalleled Data Quality
- Higher Quality Content
- 60% Fewer Hallucinations
Browse by: Latest US Patents, China's latest patents, Technical Efficacy Thesaurus, Application Domain, Technology Topic, Popular Technical Reports.
© 2025 PatSnap. All rights reserved.Legal|Privacy policy|Modern Slavery Act Transparency Statement|Sitemap|About US| Contact US: help@patsnap.com