Bearing load online monitoring method based on eddy current displacement sensor
A technology for displacement sensors and bearing loads, applied to instruments, measuring devices, and electrical devices, etc., can solve problems such as inability to directly bear force, and achieve the effects of reducing measurement difficulty, ensuring accuracy, and reducing types and quantities
- Summary
- Abstract
- Description
- Claims
- Application Information
AI Technical Summary
Problems solved by technology
Method used
Image
Examples
Embodiment Construction
[0021] The technical solutions in the embodiments of the present invention are clearly and completely described below in conjunction with the accompanying drawings.
[0022] Such as figure 1 As shown, a kind of bearing load monitoring method based on eddy current displacement sensor of the present invention, specific embodiment is as follows:
[0023] Step 1. Widen the inner ring of the bearing so that at least three sensors can be arranged in the radial and axial directions, and use the load loading test to obtain the distance between the inner ring of the bearing and the outer ring according to the distance between the sensor and the marked point on the bearing measurement surface. Radial and axial static displacement, and then obtain the angular displacement of the bearing according to the radial and axial displacement and the method of determining the spatial orientation at three points;
[0024] Step 2. Establish a quasi-static model based on the basic design parameters ...
PUM
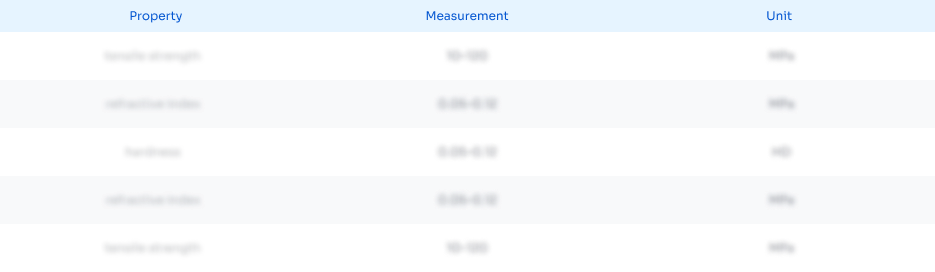
Abstract
Description
Claims
Application Information

- R&D Engineer
- R&D Manager
- IP Professional
- Industry Leading Data Capabilities
- Powerful AI technology
- Patent DNA Extraction
Browse by: Latest US Patents, China's latest patents, Technical Efficacy Thesaurus, Application Domain, Technology Topic, Popular Technical Reports.
© 2024 PatSnap. All rights reserved.Legal|Privacy policy|Modern Slavery Act Transparency Statement|Sitemap|About US| Contact US: help@patsnap.com