Method for cooperatively treating emulsified oil sludge by sintering system
A technology for co-processing and emulsification of oil, applied in the direction of improving process efficiency, etc., can solve the problems of difficult to meet the standard emission of exhaust gas, evaluation of the total amount of volatile components of sintering ingredients, and viscosity of rolling sludge.
- Summary
- Abstract
- Description
- Claims
- Application Information
AI Technical Summary
Problems solved by technology
Method used
Image
Examples
Embodiment 1
[0026] A method for co-processing emulsified oil sludge with a sintering system, such as figure 1 shown, including the following steps:
[0027] S1. Mixing: Fully mix 3.18 tons of emulsified oil sludge, 9.54 tons of water treatment sludge and 19.08 tons of iron-containing dust, and the moisture content after mixing is 18.16%;
[0028] S2. Secondary mixing: send the mixed dust and mud to the raw material storage yard with a tanker, and mix again with 47.7 tons of OG coarse grains and 79.5 tons of pellet under-sieve powder;
[0029] S3. Sintering and mixing: transport the mixed material to the sintering mixer with a belt, and mix the mixed material into the sintering raw material at a ratio of 0.5%, and go through primary mixing, secondary mixing, disc making After the ball enters two sintering machines for consumption;
[0030] S4. Dust removal: pass the sintering flue gas into the electric dust removal equipment, and use the pneumatic ash conveying equipment to send the dust...
Embodiment 2
[0033] A method for co-processing emulsified oil sludge with a sintering system, such as figure 1 shown, including the following steps:
[0034] S1. Mixing: Fully mix 1.56 tons of emulsified oil sludge, 6.24 tons of water treatment sludge and 7.8 tons of iron-containing dust, and the moisture content after mixing is 17.53%;
[0035] S2. Secondary mixing: send the mixed dust and sludge to the raw material storage yard with a tanker, and mix again with 23.4 tons of OG coarse grains and 39 tons of pelletized sieved powder;
[0036] S3. Sintering and mixing: transport the mixed material to the sintering mixer with a belt, and mix the mixed material into the sintering raw material at a ratio of 0.5%, and go through primary mixing, secondary mixing, disc making After the ball enters two sintering machines;
[0037] S4. Dust removal: pass the sintering flue gas into the electric dust removal equipment, and use the pneumatic ash conveying equipment to send the dust collected by the ...
Embodiment 3
[0040] A method for co-processing emulsified oil sludge with a sintering system, such as figure 1 shown, including the following steps:
[0041] S1. Mixing: fully mix 1.24 tons of emulsified oil sludge, 3.72 tons of water treatment sludge and 7.44 tons of iron-containing dust, and the moisture content after mixing is 15.06%;
[0042] S2. Secondary mixing: send the mixed dust and sludge to the raw material storage yard with a tanker, and mix again with 24.8 tons of OG coarse grains and 86.8 tons of pellet sieved powder;
[0043] S3. Sintering mixing: convey the mixed material to the sintering mixer with a belt, and mix the mixed material into the sintering raw material at a ratio of 0.8%, and go through primary mixing, secondary mixing, and disc making After the ball enters two sintering machines;
[0044] S4. Dust removal: the sintering flue gas enters the electric dust removal equipment, and the dust collected by the dust collector is sent to the batching room for reuse by ...
PUM
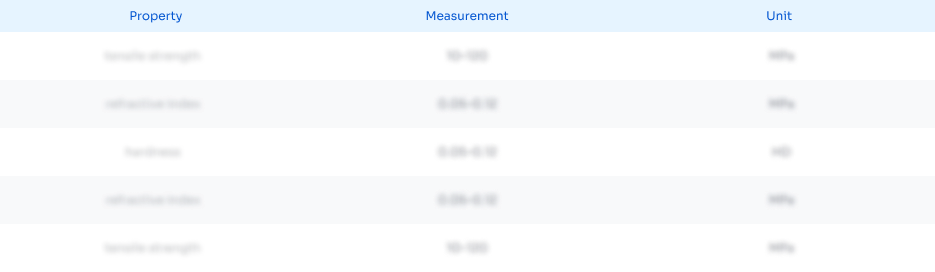
Abstract
Description
Claims
Application Information

- R&D
- Intellectual Property
- Life Sciences
- Materials
- Tech Scout
- Unparalleled Data Quality
- Higher Quality Content
- 60% Fewer Hallucinations
Browse by: Latest US Patents, China's latest patents, Technical Efficacy Thesaurus, Application Domain, Technology Topic, Popular Technical Reports.
© 2025 PatSnap. All rights reserved.Legal|Privacy policy|Modern Slavery Act Transparency Statement|Sitemap|About US| Contact US: help@patsnap.com