Preparation method of high-voltage and ultrahigh-voltage cable insulating material
A cable insulation and ultra-high voltage technology, applied in the direction of organic insulators, plastic/resin/wax insulators, etc., can solve the problems of time-consuming and labor-intensive cleaning equipment and environmental systems, high production and maintenance costs, and affect the quality of insulating materials, etc., to achieve equipment investment less, low cost, and improved cleanliness and stability
- Summary
- Abstract
- Description
- Claims
- Application Information
AI Technical Summary
Problems solved by technology
Method used
Image
Examples
Embodiment Construction
[0015] The present invention will be further described below in conjunction with the accompanying drawings.
[0016] A preparation method for high-voltage and ultra-high-voltage cable insulation materials, the specific process is as follows:
[0017] (1) After the ethylene monomer is compressed by the compressor 1, it is polymerized into low-density polyethylene at high pressure in the reactor 2. After being separated by the high-pressure and low-pressure separator 3, the low-density polyethylene directly enters the single-screw extruder 6 after being cooled. , add the liquid antioxidant 5 directly through the metering pump 4, and disperse the liquid antioxidant 5 evenly in the low-density polyethylene through the diversion device and the single-screw extruder 6, and then filter through the high-mesh filter 7 Granulate and store in the storage tank 8 to obtain antioxidant-containing low-density polyethylene. The liquid antioxidant used in this example is 2,4-bis(n-octylthiome...
PUM
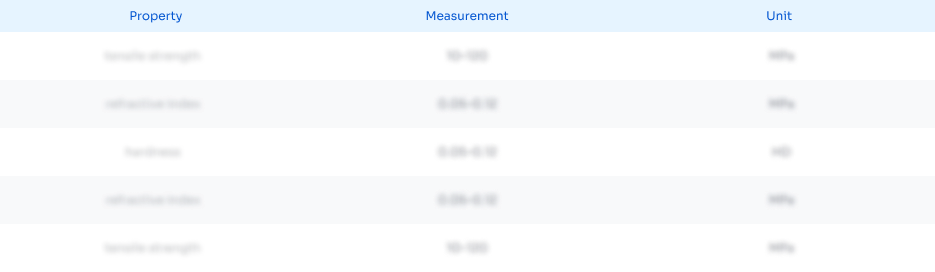
Abstract
Description
Claims
Application Information

- R&D
- Intellectual Property
- Life Sciences
- Materials
- Tech Scout
- Unparalleled Data Quality
- Higher Quality Content
- 60% Fewer Hallucinations
Browse by: Latest US Patents, China's latest patents, Technical Efficacy Thesaurus, Application Domain, Technology Topic, Popular Technical Reports.
© 2025 PatSnap. All rights reserved.Legal|Privacy policy|Modern Slavery Act Transparency Statement|Sitemap|About US| Contact US: help@patsnap.com