Digital rotary screen combined printing and dyeing equipment and operation process thereof
A technology of printing and dyeing equipment and operation process, which is applied in the field of digital rotary screen combined printing and dyeing equipment and its operation process, can solve the problems of low mass production efficiency, slow printing speed, large amount of rotary screen printing and dyeing paste, etc., so as to reduce defects. Product generation, protect working life, ensure the effect of drying and humidity
- Summary
- Abstract
- Description
- Claims
- Application Information
AI Technical Summary
Problems solved by technology
Method used
Image
Examples
Embodiment 1
[0036] Such as figure 1 A structural schematic diagram of an embodiment of the present invention is shown, a digital rotary screen combined printing and dyeing equipment, including a body, the body includes a rotary screen printing device on the front side and a digital direct-jet printing device connected to the rear end of the rotary screen printing device, and intelligent control devices.
[0037] In this embodiment, the rotary screen printing device includes a cloth feeding frame arranged at the front of the body, an overfeeding device is arranged at the rear of the cloth feeding frame, and a rotary screen device I is arranged at the rear of the overfeeding device. An oven Ⅰ is installed at the front, a rotary screen device Ⅱ is installed behind the oven, a digital printing device is installed behind the rotary screen device Ⅱ, a rotary screen device Ⅲ is installed at the rear of the digital printing device, and an oven Ⅱ is installed at the rear of the rotary screen devic...
Embodiment 2
[0059] The difference from Example 1 is that in step 3), the temperature parameter of the high temperature and high pressure is controlled at 130 degrees, and the pressure parameter is controlled at 0.35Mpa; it is predetermined that the fabric is stabilized by high temperature under tension. , the temperature is 210 degrees, the speed is 55M / min; weight reduction, through the treatment of liquid alkali, the fiber can get the expected hand feeling and coloring rate, the temperature is 95 degrees, the liquid alkalinity is 5-20%; neutralization and desizing, remove the gray cloth by high temperature Stains and other impurities, the temperature is 100 degrees, and the semi-finished product is finalized.
[0060] In step 6), finishing: steaming: steaming process, the temperature of the steaming box is 180 degrees, and the time is controlled at 8 minutes; washing: the front is washed with cold water in three water tanks, and then passed through three high-temperature water tanks, and...
PUM
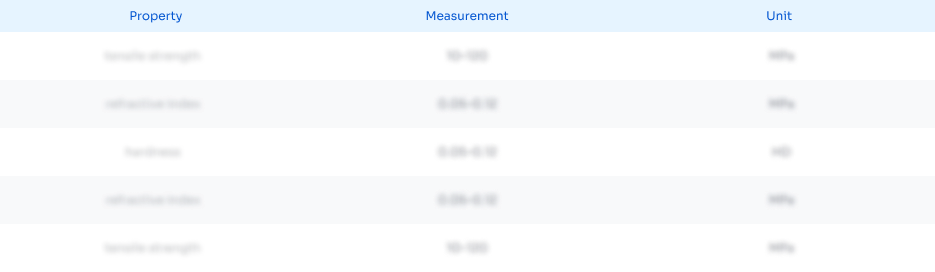
Abstract
Description
Claims
Application Information

- Generate Ideas
- Intellectual Property
- Life Sciences
- Materials
- Tech Scout
- Unparalleled Data Quality
- Higher Quality Content
- 60% Fewer Hallucinations
Browse by: Latest US Patents, China's latest patents, Technical Efficacy Thesaurus, Application Domain, Technology Topic, Popular Technical Reports.
© 2025 PatSnap. All rights reserved.Legal|Privacy policy|Modern Slavery Act Transparency Statement|Sitemap|About US| Contact US: help@patsnap.com