Granules of microwave dielectric material for injection molding, and manufacturing method of microwave dielectric device
A microwave dielectric material and injection molding technology, applied in the field of microwave dielectric materials, can solve the problems of increased process, poor uniformity of organizational structure, complex structure, etc., and achieve the effect of improving production efficiency, density and uniformity, and improving performance
- Summary
- Abstract
- Description
- Claims
- Application Information
AI Technical Summary
Problems solved by technology
Method used
Image
Examples
preparation example Construction
[0032] The embodiment of the present invention also provides a method for preparing a microwave dielectric material green body, including the following steps:
[0033] S1. Prepare a microwave dielectric material with a weight percentage of 70% to 90% and a binder of 10% to 30%, wherein the microwave dielectric material includes 60% to 70% of titanium dioxide, 25% to 35% of magnesium oxide, 2 %~8% calcium carbonate, 2%~8% barium carbonate, 0.1%~1% niobium pentoxide, 0.1%~1% bismuth trioxide; the binder includes polyoxymethylene 70%-90% , polymethyl methacrylate 2%-15%, polypropylene 2%-15%, ethylene-vinyl acetate copolymer 2%-15%, wax 2%-10%, dioctyl phthalate 1%- 3%, dibutyl phthalate 1% to 3%, stearic acid 1% to 5%;
[0034] S2, using the materials prepared in step S1 to banbury and granulate;
[0035] S3. Using the material obtained in step S2 to perform injection molding to obtain the microwave dielectric material green body.
[0036] A method for manufacturing a microwa...
Embodiment 1
[0060] Granules for injection molding are composed of the following components by weight percentage:
[0061] Microwave dielectric material 70%
[0062] Binder 30%
[0063] The microwave dielectric material is composed of the following components by weight percentage:
[0064]
[0065]
[0066] Described binding agent is made up of the component of following percentage by weight:
[0067]
[0068] Mix according to the above weight percentages and put them into the internal mixer for internal mixing, set the temperature at 180° C., set the speed of the agitator at 60 rpm, and set the time for 2 hours. After the mud is refined, it will be automatically cut into Ф5mm~Ф10mm materials in the internal mixer for later use.
[0069] Heat and melt the material in the barrel of the injection machine at 180°C, inject the molten material into the mold cavity under a pressure of 110Bar, and fill the cavity; after the cavity is filled, the heat in the material is conducted out t...
Embodiment 2
[0079] Granules for injection molding are composed of the following components by weight percentage:
[0080] Microwave dielectric material 75%
[0081] Binder 25%
[0082] The microwave dielectric material is composed of the following components by weight percentage:
[0083]
[0084] Described binding agent is made up of the component of following percentage by weight:
[0085]
[0086] Mix according to the above weight percentages and put them into an internal mixer for internal mixing, set the temperature at 185° C., set the rotational speed of the agitator at 60 rpm, and set the time for 2 hours. After the mud is refined, it will be automatically cut into Ф5mm~Ф10mm materials in the internal mixer for later use.
[0087] Heat and melt the material in the barrel of the injection machine at 185°C, inject the molten material into the mold cavity under a pressure of 115 Bar, and fill the cavity; after the cavity is filled, the heat in the material is conducted throug...
PUM
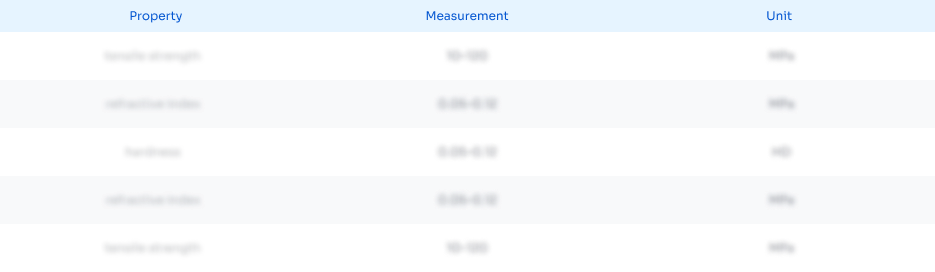
Abstract
Description
Claims
Application Information

- Generate Ideas
- Intellectual Property
- Life Sciences
- Materials
- Tech Scout
- Unparalleled Data Quality
- Higher Quality Content
- 60% Fewer Hallucinations
Browse by: Latest US Patents, China's latest patents, Technical Efficacy Thesaurus, Application Domain, Technology Topic, Popular Technical Reports.
© 2025 PatSnap. All rights reserved.Legal|Privacy policy|Modern Slavery Act Transparency Statement|Sitemap|About US| Contact US: help@patsnap.com