Copper-based low-temperature shift catalyst and preparation method thereof
A shift catalyst, low temperature technology, applied in the field of copper-based low temperature shift catalyst and preparation, can solve the problems of lower specific surface, unstable catalyst structure, easy loss of alkali metal, etc., and achieve the effect of stable performance
- Summary
- Abstract
- Description
- Claims
- Application Information
AI Technical Summary
Problems solved by technology
Method used
Image
Examples
Embodiment 1
[0029] Will Cu 2+ Cu(NO 3 ) 2 Solution 2L, Zn 2+ Zn(NO 3 ) 2 Solution 0.6L, configured in a neutralization tank as a mixed solution 1, heated to 70°C under stirring;
[0030] Dilute 100g of JA-25 silica sol to 400mL to form solution 2;
[0031] Add solution 2 into solution 1 and stir well to form solution 3;
[0032] Prepare Na in the alkali tank 2 CO 3 Alkaline solution, 0.1Kg of soda ash per liter of water is made into precipitant solution 4;
[0033] Solution 4 was added to solution 3, and the end point pH value was 7.8 to form slurry 1;
[0034] Weigh 50g of pseudo-boehmite, add 50g of magnesium oxide powder into slurry 1, and beat for 20min.
[0035] After the slurry I after beating is filtered, washed and dried, K is added 2 CO 3 10 g was ground and granulated, calcined at 450° C., added graphite and pressed into pellets to obtain the catalyst.
Embodiment 2
[0037] Will Cu 2+ Cu(NO 3 ) 2 Solution 4L, Zn 2+ Zn(NO 3 ) 2 Solution 1.6L, configured in a neutralization tank as a mixed solution 1, heated to 70°C under stirring;
[0038] Dilute 100g of JA-25 silica sol to 400mL to form solution 2;
[0039] Add solution 2 into solution 1 and stir well to form solution 3;
[0040] Prepare Na in the alkali tank 2 CO 3 Alkaline solution, 0.1Kg of soda ash per liter of water is made into precipitant solution 4;
[0041] Solution 4 was added to solution 3, and the end point pH value was 7.8 to form slurry 1;
[0042] Weigh 25g of magnesia-alumina spinel and add it into the slurry 1, beat for 20min.
[0043] After the beating slurry 1 was filtered, washed and dried, CaCO was added 3 10g, K 2 CO 3 10 g was ground and granulated, calcined at 500° C., added graphite and pressed into pellets to obtain the catalyst.
Embodiment 3
[0045] Will Cu 2+ Cu(NO 3 ) 2 Solution 2L, Zn 2+ Zn(NO 3 ) 2 Solution 0.5L, configured in a neutralization barrel to form a mixed solution 1, heated to 60°C under stirring;
[0046] Dilute 150g of JA-25 silica sol to 400mL to form solution 2;
[0047] Add solution 2 into solution 1 and stir well to form solution 3;
[0048] Prepare Na in the alkali tank 2 CO 3 Alkaline solution, 0.1Kg of soda ash per liter of water is made into precipitant solution 4;
[0049]Solution 4 was added to solution 3, and the end point pH value was 7.2 to form slurry 1;
[0050] Weigh 200g of pseudo-boehmite and 70g of magnesium oxide powder into the slurry 1, beat for 20min.
[0051] After the beating slurry 1 was filtered, washed and dried, CaCO was added 3 10 g was ground and granulated, calcined at 420° C., and graphite was added to form a tablet to obtain the catalyst.
PUM
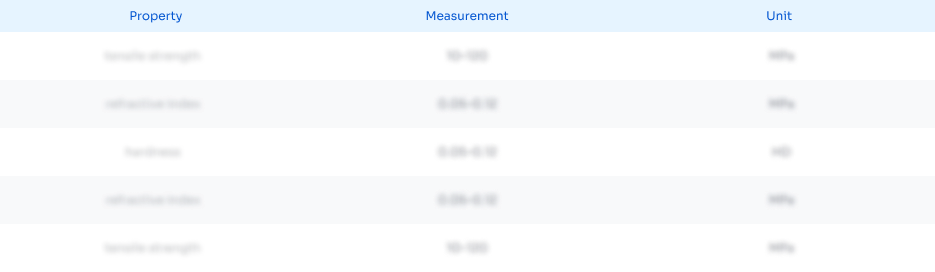
Abstract
Description
Claims
Application Information

- R&D
- Intellectual Property
- Life Sciences
- Materials
- Tech Scout
- Unparalleled Data Quality
- Higher Quality Content
- 60% Fewer Hallucinations
Browse by: Latest US Patents, China's latest patents, Technical Efficacy Thesaurus, Application Domain, Technology Topic, Popular Technical Reports.
© 2025 PatSnap. All rights reserved.Legal|Privacy policy|Modern Slavery Act Transparency Statement|Sitemap|About US| Contact US: help@patsnap.com