Design and additive manufacturing method of gradient porous structure heat dissipation device based on temperature distribution
A temperature distribution, additive manufacturing technology, applied in the direction of additive processing, process efficiency improvement, energy efficiency improvement, etc., can solve problems such as no gradient design, reduce manufacturing cycle, improve heat transfer efficiency, eliminate welding requirements and The effect of assembly defects
- Summary
- Abstract
- Description
- Claims
- Application Information
AI Technical Summary
Problems solved by technology
Method used
Image
Examples
Embodiment Construction
[0039] The technical solutions in the embodiments of the present invention will be described clearly and in detail below with reference to the drawings in the embodiments of the present invention. The described embodiments are only some of the embodiments of the invention.
[0040] The technical scheme that the present invention solves the problems of the technologies described above is:
[0041] Working principle and process:
[0042] Facing the heat exchanger's demand for high efficiency, compactness and light weight, the present invention proposes a gradient porous structure design method based on temperature distribution and a 3D printing manufacturing method. The way to achieve it is as figure 1 Shown:
[0043] 1. First collect the temperature distribution of the heating element, and establish the spatial matrix of the temperature distribution.
[0044] 2. Select a TPMS porous structure, and use the gradient algorithm to control the relative density of the porous stru...
PUM
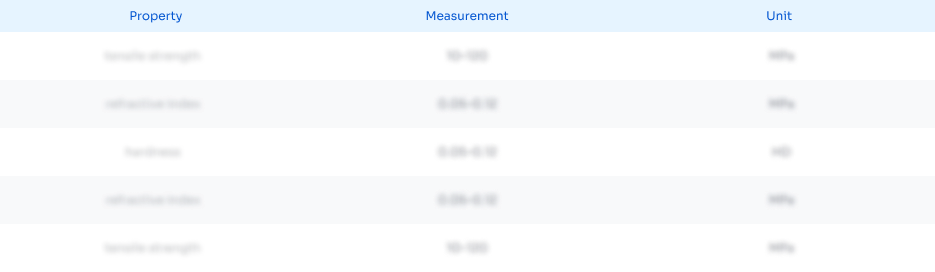
Abstract
Description
Claims
Application Information

- R&D
- Intellectual Property
- Life Sciences
- Materials
- Tech Scout
- Unparalleled Data Quality
- Higher Quality Content
- 60% Fewer Hallucinations
Browse by: Latest US Patents, China's latest patents, Technical Efficacy Thesaurus, Application Domain, Technology Topic, Popular Technical Reports.
© 2025 PatSnap. All rights reserved.Legal|Privacy policy|Modern Slavery Act Transparency Statement|Sitemap|About US| Contact US: help@patsnap.com