Method for denitrifying calcined flue gas of magnesite clinker
A technology of sintered magnesia and calcination, which is applied in the field of denitrification of sintered magnesia calcination flue gas, can solve the problems of high cost and low efficiency, and achieve the effects of reducing load, high denitrification efficiency, and reducing investment and operating costs
- Summary
- Abstract
- Description
- Claims
- Application Information
AI Technical Summary
Problems solved by technology
Method used
Image
Examples
Embodiment Construction
[0032] The present invention proposes a method for denitrification of flue gas from sintered magnesia calcination based on source reduction, process control and end treatment:
[0033] (1) Use natural gas and other clean fuels instead of unclean fuels to reduce or avoid the generation of fuel-type nitrogen oxides from the source;
[0034] (2) Arrange two-stage burners at suitable positions on the shaft furnace, namely the main calciner burner and the secondary calciner burner, to realize the staged combustion of fuel. Keep the ratio of the height of the material layer above the center line of the main calcination burner to the height of the material layer below the center line of the burner within 0.49 to 0.58, and arrange the secondary calcination burner above the center line of the main calcination burner, and control the calcination section and cooling section of the shaft furnace The gas-solid-water equivalent ratio is 0.8.
[0035] The natural gas is sent to the main cal...
PUM
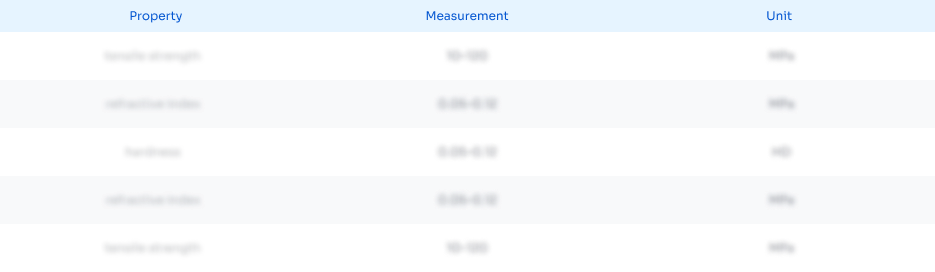
Abstract
Description
Claims
Application Information

- Generate Ideas
- Intellectual Property
- Life Sciences
- Materials
- Tech Scout
- Unparalleled Data Quality
- Higher Quality Content
- 60% Fewer Hallucinations
Browse by: Latest US Patents, China's latest patents, Technical Efficacy Thesaurus, Application Domain, Technology Topic, Popular Technical Reports.
© 2025 PatSnap. All rights reserved.Legal|Privacy policy|Modern Slavery Act Transparency Statement|Sitemap|About US| Contact US: help@patsnap.com