Composite sludge conditioner
A sludge conditioner and conditioner technology, which is applied in sludge treatment, water/sludge/sewage treatment, chemical instruments and methods, etc., can solve the problems of not achieving dehydration effect and increasing the difficulty of sludge dehydration, and achieve structural Dense, strong shear resistance, not easy to break
- Summary
- Abstract
- Description
- Claims
- Application Information
AI Technical Summary
Problems solved by technology
Method used
Examples
Embodiment 1
[0024] Mix 150 g of polyaluminum chloride, 100 g of β-cyclodextrin-polyacrylamide polymer, 200 g of dodecyldimethylammonium chloride, 150 g of sodium bicarbonate, and 400 g of fly ash, and mix them at room temperature Blast drying under the conditions for 30 minutes, crushed to 50-200 mesh, and made into composite sludge conditioner.
[0025] Add the composite sludge conditioner of this embodiment to the sludge with a water content of 98%. The amount of the composite sludge conditioner is 10% of the absolute dry weight of the sludge. Stir for 30 min and press with a plate and frame filter press. Filtration and dehydration, the dehydration pressure is 1.5 Mpa, the dehydration and filtration time is 30 minutes, and then the pressure is released and the material is discharged. The moisture content of the test sludge is 37%.
Embodiment 2
[0027] Mix 200 g of polyferric sulfate, 150 g of β-cyclodextrin-polyacrylamide polymer, 100 g of cetyltrimethylammonium bromide, 200 g of sodium carbonate, and 350 g of fly ash. Blow drying for 30 minutes, crush to 50-200 mesh, and make composite sludge conditioner.
[0028] Add the composite sludge conditioner of this embodiment to the sludge with a water content of 98%. The amount of the composite sludge conditioner is 10% of the absolute dry weight of the sludge. Stir for 30 min and press with a plate and frame filter press. Filtration and dehydration, the dehydration pressure is 1.5 Mpa, the dehydration and filtration time is 30 minutes, and then the pressure is released and the material is discharged. The moisture content of the test sludge is 43%.
Embodiment 3
[0030] Polyferric sulfate 100 g, polyaluminum chloride 150 g, β-cyclodextrin-polyacrylamide polymer 50 g, dodecyl dimethyl ammonium chloride 150 g, sodium carbonate 50 g, sodium bicarbonate 150 g g. 350 g of fly ash was mixed thoroughly, blown and dried for 30 minutes at room temperature, and crushed to 50-200 mesh to make a composite sludge conditioner.
[0031] Add the composite sludge conditioner of this embodiment to the sludge with a water content of 98%. The amount of the composite sludge conditioner is 10% of the absolute dry weight of the sludge. Stir for 30 min and press with a plate and frame filter press. Filtration and dehydration, the dehydration pressure is 1.5 Mpa, the dehydration and filtration time is 30 minutes, and then the pressure is released and the material is discharged. The moisture content of the test sludge is 44%.
PUM
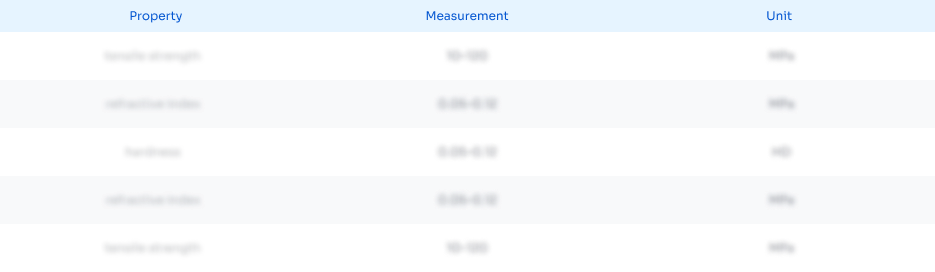
Abstract
Description
Claims
Application Information

- R&D Engineer
- R&D Manager
- IP Professional
- Industry Leading Data Capabilities
- Powerful AI technology
- Patent DNA Extraction
Browse by: Latest US Patents, China's latest patents, Technical Efficacy Thesaurus, Application Domain, Technology Topic, Popular Technical Reports.
© 2024 PatSnap. All rights reserved.Legal|Privacy policy|Modern Slavery Act Transparency Statement|Sitemap|About US| Contact US: help@patsnap.com