Method for continuously synthesizing methyl isopropyl ketone
A methyl isopropyl ketone, chemical synthesis technology, applied in the direction of chemical instruments and methods, preparation of organic compounds, carbon-based compounds, etc., can solve the problems of high operating costs, low production efficiency, unfavorable industrial production, etc., to achieve Reduce operating costs, realize automatic control, and reduce the effect of manual operations
- Summary
- Abstract
- Description
- Claims
- Application Information
AI Technical Summary
Problems solved by technology
Method used
Image
Examples
Embodiment 1
[0022]Replace the four-stage 1L series hydrogenation reactor with nitrogen for three times and hydrogen for three times, and maintain the hydrogen pressure of the reactors at 0.2Mpa. Turn on methyl ethyl ketone, catalyst feed pump and formaldehyde feed pump to start feeding the first-stage kettle; the flow rate of methyl ethyl ketone is 6.3g / min, the flow rate of formaldehyde solution (37%) is 6.42g / min, catalyst slurry The flow rate is 0.31g / min.
[0023]Turn on the self-priming and stirring of the first-stage kettle (rotating speed 650 rpm), and control the temperature of the first-stage to 35-40℃; when the material in the first-stage kettle reaches the overflow level, it will flow into the second-stage kettle and turn on the second-stage kettle Self-priming stirring (rotating speed 650 rpm), controlling temperature 60-65℃; when the liquid level of the second tank reaches the overflow level, the material starts to enter the third-stage kettle, and turning on the third-stage tank stir...
Embodiment 2
[0025]Replace the five-stage 1L series hydrogenation reactor with nitrogen for three times and hydrogen for three times, and maintain the hydrogen pressure of the reactors at 3.0Mpa. Turn on the methyl ethyl ketone, catalyst feed pump and formaldehyde feed pump to start feeding the first-stage kettle. The flow rate of methyl ethyl ketone is 6.3g / min; the flow rate of formaldehyde solution (37%) is 5g / min; the flow rate of catalyst slurry is 0.31g / min.
[0026]Turn on the self-priming stirring of the first-stage kettle (rotational speed 360 rpm), control the first-stage temperature to 35-40℃; when the first-stage kettle material reaches the overflow level, start to flow into the second-stage kettle, and turn on the second-stage kettle Self-priming stirring (rotating speed 650 rpm), temperature control 65-70℃; when the liquid level of the second tank reaches the overflow level, the material starts to enter the third-stage tank, and the third-stage tank stirring is started (rotating speed...
Embodiment 3
[0028]Replace the three-stage 1L series hydrogenation reactor with nitrogen for three times and hydrogen for three times, and keep the hydrogen pressure of the reactors at 4.0Mpa. Turn on the methyl ethyl ketone, catalyst feed pump and formaldehyde feed pump to start feeding the first-stage kettle.
[0029]The first-stage kettle is fed, the flow rate of methyl ethyl ketone is 6.3g / min; the flow rate of formaldehyde solution (37%) is 2g / min; the flow rate of catalyst slurry is 0.25g / min; the first-stage kettle self-priming stirring (speed 860 rpm), control the first-stage temperature to 40-45°C, when the material reaches the overflow level of the first-stage kettle, start to enter the second-stage kettle, and turn on the second-stage kettle to stir (speed 650 rpm) , Keep the temperature of the second-stage kettle at 55-60℃, when the material liquid reaches the overflow level of the first-stage kettle, start to enter the third-stage kettle, turn on the third-stage kettle to stir (speed 6...
PUM
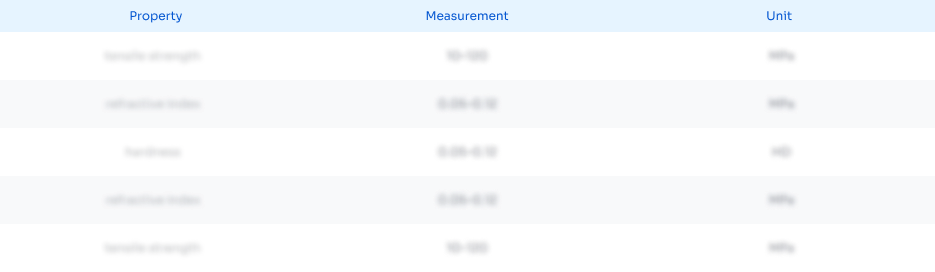
Abstract
Description
Claims
Application Information

- Generate Ideas
- Intellectual Property
- Life Sciences
- Materials
- Tech Scout
- Unparalleled Data Quality
- Higher Quality Content
- 60% Fewer Hallucinations
Browse by: Latest US Patents, China's latest patents, Technical Efficacy Thesaurus, Application Domain, Technology Topic, Popular Technical Reports.
© 2025 PatSnap. All rights reserved.Legal|Privacy policy|Modern Slavery Act Transparency Statement|Sitemap|About US| Contact US: help@patsnap.com