Molybdenum disulfide anticorrosive coating based on electrochemical deposition and preparation process thereof
A technology of molybdenum disulfide and anti-corrosion coating, which is applied in coatings, electrolytic coatings, etc., can solve the problems of shortening service life, safety accidents, reducing the mechanical properties of metal materials such as strength, plasticity, and toughness, etc., to improve comprehensive performance, Promotes lubricity and enhances lubricity
- Summary
- Abstract
- Description
- Claims
- Application Information
AI Technical Summary
Problems solved by technology
Method used
Image
Examples
Embodiment 1
[0031] Take nano-scale graphite, place it in the plating solution, soak it at 50°C for 5 minutes, heat up to 400°C for electroplating, the plating time is 13 minutes, the plating current is 3A, and then cooled to 250°C at a speed of 15°C / s , cooled to room temperature at a rate of 5°C / s, taken out and dried to obtain modified graphite; the plating solution contained 70 parts of pure water, 30 parts of water-based acrylic resin, 9.2 parts of zinc chloride, 0.5 parts of aluminum chloride, 0.1 Parts of nano-nickel particles, 5 parts of sodium chloride, 2 parts of chromium trioxide;
[0032] Get 27 parts of molybdenum pentachloride, 6.5 parts of elemental sulfur and add to the solvent, add 0.5 parts of sodium dodecylbenzenesulfonate, 3 parts of n-dodecyl mercaptan, 0.8 parts of polyoxyethylene sorbitan monooleate, 3 parts Parts of nano-graphite particles are mixed uniformly and fully stirred to obtain an electrolyte solution; graphite is taken as an anode electrode, and the materi...
Embodiment 2
[0035] Take nano-scale graphite, place it in the plating solution, soak it at 57°C for 7 minutes, heat up to 415°C for electroplating, the plating time is 17 minutes, the plating current is 6A, and then cooled to 265°C at a speed of 32°C / s , cooled to room temperature at a rate of 5-10°C / s, taken out and dried to obtain modified graphite; the plating solution contained 82 parts of pure water, 17 parts of water-based acrylic resin, 9.3 parts of zinc chloride, and 0.6 parts of aluminum chloride , 0.5 parts of nano nickel particles, 12 parts of sodium chloride, 8 parts of chromium trioxide;
[0036] Take 34 parts of molybdenum pentachloride and 8 parts of elemental sulfur and add them to the solvent, add 0.7 parts of sodium dodecylbenzenesulfonate, 3.5 parts of n-dodecyl mercaptan, 1.2 parts of polyoxyethylene sorbitan monooleate, 3.5 parts Parts of nano-graphite particles are mixed uniformly and fully stirred to obtain an electrolyte solution; graphite is taken as an anode elect...
Embodiment 3
[0039] Take nano-scale graphite, place it in the plating solution, soak it at 65°C for 10 minutes, heat up to 430°C for electroplating, the plating time is 21 minutes, the plating current is 0A, and then cooled to 280°C at a speed of 50°C / s , cooled to room temperature at a rate of 10°C / s, taken out and dried to obtain modified graphite; the plating solution contained 95 parts of pure water, 30 parts of water-based acrylic resin, 9.5 parts of zinc chloride, 0.8 parts of aluminum chloride, 1 Parts of nano-nickel particles, 20 parts of sodium chloride, 15 parts of chromium trioxide;
[0040]Get 41 parts of molybdenum pentachloride, 9.6 parts of elemental sulfur and add in the solvent, add 1.0 parts of sodium dodecylbenzenesulfonate, 4 parts of n-dodecyl mercaptan, 1.6 parts of polyoxyethylene sorbitan monooleate, 4 parts Parts of nano-graphite particles are mixed uniformly and fully stirred to obtain an electrolyte solution; graphite is taken as an anode electrode, and the mater...
PUM
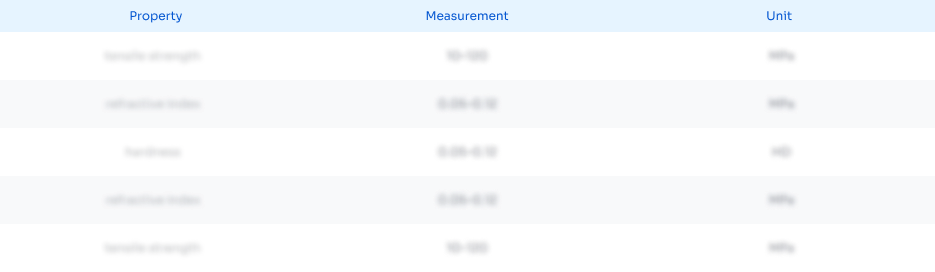
Abstract
Description
Claims
Application Information

- R&D
- Intellectual Property
- Life Sciences
- Materials
- Tech Scout
- Unparalleled Data Quality
- Higher Quality Content
- 60% Fewer Hallucinations
Browse by: Latest US Patents, China's latest patents, Technical Efficacy Thesaurus, Application Domain, Technology Topic, Popular Technical Reports.
© 2025 PatSnap. All rights reserved.Legal|Privacy policy|Modern Slavery Act Transparency Statement|Sitemap|About US| Contact US: help@patsnap.com