Air reservoir adopting composite material
A composite material and air storage cylinder technology, which is applied in the field of composite material air storage cylinders, can solve the problems of axial and radial winding, weakened welding line strength, weak strength at the end cover, etc., and achieves the effect of ensuring safety strength
- Summary
- Abstract
- Description
- Claims
- Application Information
AI Technical Summary
Problems solved by technology
Method used
Image
Examples
Embodiment 1
[0029] like Figure 1-7 As shown, in a composite material air storage tank of the present invention, inserts B are arranged at the ends of both sides of the liner A, and an exhaust pipe joint C and a drain pipe joint D are arranged on the insert B, and the internal drain pipe E is connected to the drain On the pipe joint D, the end of the internal drain pipe E is connected to the bottom of the air storage tank, and the outer layer is a fiber resin composite winding layer, and the fiber resin composite winding layer includes an axial winding layer H and a radial winding layer G (that is, using axial winding and radial winding).
[0030] In this embodiment, three threaded holes are preset on the insert B, such as figure 2 As shown in the equiangular arrangement, the insert B is buried in the mold in advance, and is injection molded together with the liner A. The material of the liner A is nylon 66+GF33 material, as shown in image 3 As shown, the welding boss 1 in the liner A...
Embodiment 2
[0035] A composite material air storage tank, inserts B are arranged on both sides of the inner tank A, and an exhaust pipe joint C and a drain pipe joint D are arranged on the insert B. The internal drain pipe E is connected to the drain pipe joint D, and the internal The end of the drain pipe E is connected to the bottom of the air storage tank, the outer layer is a fiber resin composite winding layer, and the fiber resin composite winding layer includes an axial winding layer H and a radial winding layer G (that is, using axial winding and radial winding).
[0036] In this embodiment, three threaded holes are preset on the insert B, such as figure 2 As shown in the equiangular arrangement, the insert B is buried in the mold in advance, and is injection molded together with the liner A. The material of the liner A is nylon 6+GF25 material, combined with Image 6 , the welding boss I in the liner is arranged inwardly.
[0037] The liner A consists of two halves. The two hal...
Embodiment 3
[0041] A composite material air storage tank, inserts B are arranged on both sides of the inner tank A, and an exhaust pipe joint C and a drain pipe joint D are arranged on the insert B. The internal drain pipe E is connected to the drain pipe joint D, and the internal The end of the drain pipe E is connected to the bottom of the air storage tank, the outer layer is a fiber resin composite winding layer, and the fiber resin composite winding layer includes an axial winding layer H and a radial winding layer G (that is, using axial winding and radial winding).
[0042] In this embodiment, three threaded holes are preset on the insert B, such as figure 2 Arranged at equal angles as shown, insert B is buried in the mold in advance, and blow molded together with liner A. The material of liner A is PE material. The surface of the liner A is polished once with 800-mesh sandpaper, and then the fiber is wound on the surface of the liner. In this embodiment, the material for the windi...
PUM
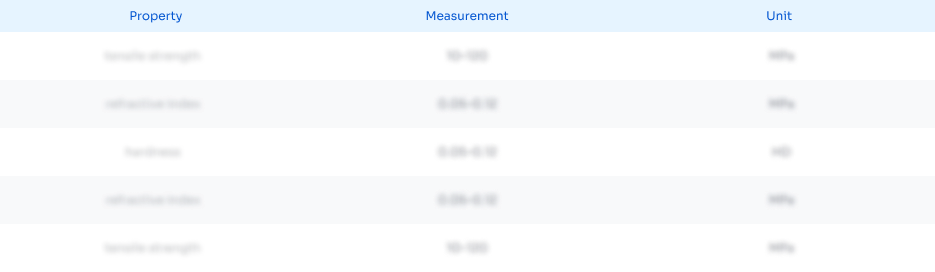
Abstract
Description
Claims
Application Information

- Generate Ideas
- Intellectual Property
- Life Sciences
- Materials
- Tech Scout
- Unparalleled Data Quality
- Higher Quality Content
- 60% Fewer Hallucinations
Browse by: Latest US Patents, China's latest patents, Technical Efficacy Thesaurus, Application Domain, Technology Topic, Popular Technical Reports.
© 2025 PatSnap. All rights reserved.Legal|Privacy policy|Modern Slavery Act Transparency Statement|Sitemap|About US| Contact US: help@patsnap.com