Concrete surface retarder as well as preparation method and application thereof
A concrete surface and retarder technology, applied in the field of cement admixtures, can solve problems such as poor high-temperature hydration inhibition effect, poor performance of surface retarders, and weakened temperature adaptability, so as to broaden the scope of use and improve high-temperature performance Performance, the effect of improving adaptability
- Summary
- Abstract
- Description
- Claims
- Application Information
AI Technical Summary
Problems solved by technology
Method used
Examples
Embodiment 1
[0031] The concrete preparation steps of present embodiment surface retarder are as follows:
[0032] 1. Preparation of polymer retarder: Add 10kg of maleic acid, 15kg of acrylic acid, and 24kg of 2-acrylamide-2-methylpropanesulfonic acid into 50kg of deionized water, dissolve, stir evenly, pass nitrogen gas for 15min, and heat up to 60 ℃, add 1 kg of potassium persulfate, and react for 2 hours to prepare a polymer retarder with a total solid content of 50%.
[0033] 2. Mix liquid raw materials: Weigh 730kg of deionized water, 5kg of borax, 50kg of 2-hydroxyphosphonoacetic acid, and 100kg of polymer retarder in a 1t stirred tank, and stir for 5min.
[0034] 3. Dissolve solid raw materials: Weigh 100kg of sodium gluconate and 5kg of calcium nitrite into the mixed solution obtained in step 2, and stir for 30 minutes until the solution is transparent and clear.
[0035] 4. Dissolved solid thickener: Weigh 10kg of cornstarch, slowly add to the solution obtained in step 3, and sti...
Embodiment 2
[0039] The concrete preparation steps of present embodiment surface retarder are as follows:
[0040] 1. Preparation of polymer retarder: Add 9kg of maleic acid, 10kg of acrylic acid, and 30kg of 2-acrylamide-2-methylpropanesulfonic acid into 50kg of deionized water, dissolve, stir evenly, pass nitrogen gas for 15min, and heat up to At 60°C, add 1 kg of potassium persulfate and react for 2 hours to prepare a polymer retarder with a total solid content of 50%.
[0041] 2. Mix liquid raw materials: Weigh 730kg of deionized water, 5kg of borax, 50kg of aminotrimethylene phosphonic acid, and 100kg of polymer retarder in a 1t stirred tank, and stir for 5 minutes.
[0042] 3. Dissolving solid raw materials: Weigh 100kg of sucrose and 5kg of calcium nitrite into the mixed solution obtained in step 2, and stir for 30 minutes until the solution is transparent and clear.
[0043] 4. Dissolved solid thickener: Weigh 10kg of cornstarch, slowly add to the solution obtained in step 3, and ...
Embodiment 3
[0047] The concrete preparation steps of present embodiment surface retarder are as follows:
[0048] 1. Preparation of polymer retarder: Add 5kg of maleic acid, 10kg of acrylic acid, and 34kg of 2-acrylamide-2-methylpropanesulfonic acid into 50kg of deionized water, dissolve, stir evenly, pass nitrogen gas for 15min, and heat up to At 60°C, add 1 kg of potassium persulfate and react for 2 hours to prepare a polymer retarder with a total solid content of 50%.
[0049] 2. Mix liquid raw materials: Weigh 730kg of deionized water, 5kg of borax, 50kg of ethylenediaminetetramethylenephosphonic acid, and 100kg of polymer retarder acid, place them in a 1t stirring tank, and stir for 5min.
[0050] 3. Dissolving solid raw materials: Weigh 100kg of sucrose and 5kg of sodium oxalate into the mixed solution obtained in step 2, and stir for 30 minutes until the solution is transparent and clear.
[0051] 4. Dissolved solid thickener: Weigh 10kg of xanthan gum, slowly add to the solution ...
PUM
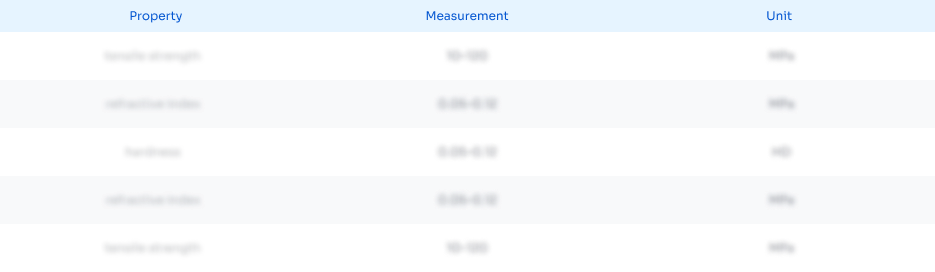
Abstract
Description
Claims
Application Information

- R&D
- Intellectual Property
- Life Sciences
- Materials
- Tech Scout
- Unparalleled Data Quality
- Higher Quality Content
- 60% Fewer Hallucinations
Browse by: Latest US Patents, China's latest patents, Technical Efficacy Thesaurus, Application Domain, Technology Topic, Popular Technical Reports.
© 2025 PatSnap. All rights reserved.Legal|Privacy policy|Modern Slavery Act Transparency Statement|Sitemap|About US| Contact US: help@patsnap.com