Method for forming special-shaped nozzle through single-engineering special-shaped part mold
A technology for mold forming and special-shaped parts, which is applied in the field of nozzle forming molds and processes, can solve problems such as pulling cracks and affect the yield of finished products, and achieve the effects of improving plasticity, improving yield and reducing stress concentration.
- Summary
- Abstract
- Description
- Claims
- Application Information
AI Technical Summary
Problems solved by technology
Method used
Image
Examples
Embodiment 1
[0027] Such as figure 1 As shown, a method for forming a special-shaped nozzle with a single-engineering special-shaped mold, including six sets of molds, followed by a flange cylinder first drawing die, a flange cylinder second drawing die, a flange cone drawing die, and a flange Special-shaped stretching die, bottom rectangular stretching die and overall shaping die, the process steps are as follows:
[0028] Step 1. Initial stretching of the cylinder: Install the cut circular plate on the working platform of the press where the flange cylinder-drawing die is located, and perform initial flange rounding on the circular plate through the flange cylinder-drawing die. Once the cylinder is stretched, the half-finished product of the flange cylinder is obtained;
[0029] Step 2. Stretch the cylinder again: take off half of the finished flange cylinder and move it to the working platform of the press where the flange cylinder second stretching mold is located. Half of the finis...
Embodiment 2
[0036] On the basis of Example 1, the following improvements were made: in step five, preheat the semi-finished flange shaped semi-finished product before stretching to a temperature of 210°C.
[0037] In a further preferred solution of the present invention, after the stretching is completed, the bottom rectangular stretching mold is cooled before being separated from the bottom rectangular stretched semi-finished product, and the cooling rate is 13° C. every ten seconds.
[0038] The invention preheats the flange semi-finished product before stretching. When the preheating temperature is 150°C to 250°C, the plasticity of the workpiece can be greatly improved, the cracking phenomenon in the stretching process can be avoided, and the stretched finished product can be greatly improved. At the same time, cool down after stretching and reduce it by 10°C to 15°C every ten seconds to prevent recrystallization inside the workpiece and improve the stretching quality.
Embodiment 3
[0040] On the basis of Example 1, the following improvements are made: the temperature difference between the upper mold and the lower mold of the six sets of molds is 60°C to 130°C, preferably 124°C, and the upper mold and the corresponding lower mold are in a constant temperature state .
[0041] The invention utilizes the constant temperature between the upper mold and the lower mold of the six sets of molds and the temperature difference is 60°C to 130°C, which can reduce the transformation of internal austenite to martensite, effectively reduce stress accumulation, and avoid hardening of stainless steel materials become brittle, thus effectively improving the quality of the stretch.
PUM
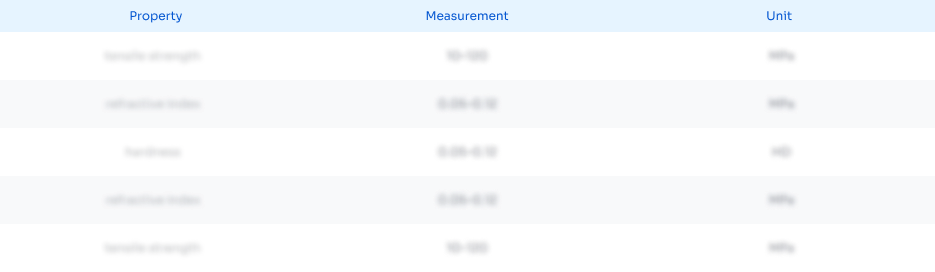
Abstract
Description
Claims
Application Information

- R&D
- Intellectual Property
- Life Sciences
- Materials
- Tech Scout
- Unparalleled Data Quality
- Higher Quality Content
- 60% Fewer Hallucinations
Browse by: Latest US Patents, China's latest patents, Technical Efficacy Thesaurus, Application Domain, Technology Topic, Popular Technical Reports.
© 2025 PatSnap. All rights reserved.Legal|Privacy policy|Modern Slavery Act Transparency Statement|Sitemap|About US| Contact US: help@patsnap.com