Rotating disk granulation device and producing process thereof
A technology of granulation equipment and production process, applied in the field of rotary disk granulation equipment and its production process, can solve the problems of low product quality, cumbersome production technology and high cost, achieve low production cost, reduce the probability of being polluted, and reduce production costs. safe effect
- Summary
- Abstract
- Description
- Claims
- Application Information
AI Technical Summary
Problems solved by technology
Method used
Image
Examples
Embodiment 1
[0036] Such as figure 1 As shown, the raw materials are placed in the liquid storage area 2 in the intermediate frequency furnace 1 for smelting. According to the target requirements, the materials in the intermediate frequency furnace can be fed multiple times to make the raw materials form molten steel. The heated guide tube 6 of the molten steel flows into the rotating disk system 9 at a certain temperature after being heated by the rotating disk heating system 8. According to the particle size and shape requirements of the metal balls, the rotation speed of the rotating disk can be adjusted to change the centrifugal force. Under the action of centrifugal force and the diversion of the rotating disk system 9, a large bundle of molten steel is thrown into a uniform droplet shape. Under the action of gravity, the droplet falls in a parabolic form. During the falling process, the droplet is under the action of surface tension. Metal balls are formed; there is a cooling medium ...
Embodiment 2
[0038] Such as figure 2As shown, the raw materials are smelted in the intermediate frequency furnace 1, and then poured into the intermediate insulation bag 17, through the guide tube 6, the guide tube heating system 7, the rotating disk heating system 8 and the rotating disk system 9 are turned on, and the liquid flows from the guide pipe Flow down the tube 6 and enter the rotary disk system 8 of the granulation area 12, adjust the rotation speed of the rotary disk system 8, the liquid is thrown out from the rotary disk system 8, and the flow is divided in the rotary disk system 8, and uniform droplets are formed under the action of centrifugal force and gravity , falling into the cooling separation area; the liquid droplets enter the cooling separation area, cool and form during the falling process, enter the material distribution area 18, turn on the cyclone separation system 21 and the induced draft fan 27, and collect the forming liquid droplets in stages, and a part of t...
PUM
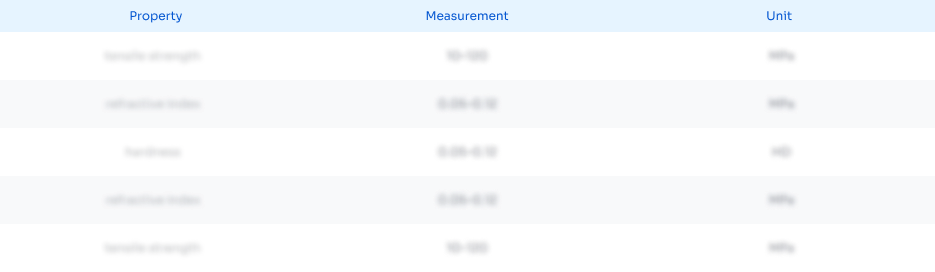
Abstract
Description
Claims
Application Information

- R&D Engineer
- R&D Manager
- IP Professional
- Industry Leading Data Capabilities
- Powerful AI technology
- Patent DNA Extraction
Browse by: Latest US Patents, China's latest patents, Technical Efficacy Thesaurus, Application Domain, Technology Topic, Popular Technical Reports.
© 2024 PatSnap. All rights reserved.Legal|Privacy policy|Modern Slavery Act Transparency Statement|Sitemap|About US| Contact US: help@patsnap.com