Industrial filter cloth cleaning process
A filter cloth and industrial technology, applied in the field of industrial filter cloth cleaning technology, can solve the problems of poor air quality, short service life of filter cloth, filter failure, etc., and achieve the effect of improving the removal effect and restoring the filter effect.
- Summary
- Abstract
- Description
- Claims
- Application Information
AI Technical Summary
Problems solved by technology
Method used
Image
Examples
Embodiment 1
[0096] An industrial filter cloth cleaning process comprises the following steps:
[0097] (1) Rinse with water:
[0098] Put the oily industrial filter cloth into the cleaning room, and use a water gun to wash the surface of the industrial filter cloth to remove large particles of oil and stains on the surface of the industrial filter cloth; the surface washing time is 20 minutes.
[0099] (2) Preparation of sludge solution:
[0100] Add the activated sludge to the salt solution, stir at a speed of 500r / min for 40min, then keep the heat preservation and stand for 4 hours at 30°C, filter to remove large particles of solid impurities, and obtain the filtrate as sludge liquid; the activated sludge and salt The solution mixing mass ratio is 100g: 1000mL. The salt solution is sodium lauryl sulfate solution; the mass fraction of sodium lauryl sulfate solution is 1.2%.
[0101] (3) Sludge liquid treatment:
[0102] Add the washed industrial filter cloth in step (1) to the sludge...
Embodiment 2
[0108] An industrial filter cloth cleaning process comprises the following steps:
[0109] (1) Rinse with water:
[0110] Put the oily industrial filter cloth into the cleaning room, and use a water gun to wash the surface of the industrial filter cloth to remove large particles of oil and stains on the surface of the industrial filter cloth; the surface washing time is 25 minutes.
[0111] (2) Preparation of sludge solution:
[0112] Add the activated sludge to the salt solution, stir at a speed of 500r / min for 40min, then keep the temperature at 34°C for 5 hours, filter to remove large particles of solid impurities, and obtain the filtrate as sludge liquid; the activated sludge and salt The solution mixing mass ratio is 150g:1000mL. The salt solution is sodium lauryl sulfate solution; the mass fraction of sodium lauryl sulfate solution is 1.2%.
[0113] (3) Sludge liquid treatment:
[0114] Add the washed industrial filter cloth in step (1) to the sludge solution, stir a...
Embodiment 3
[0120] An industrial filter cloth cleaning process comprises the following steps:
[0121] (1) Rinse with water:
[0122] Put the oily industrial filter cloth into the cleaning room, and use a water gun to wash the surface of the industrial filter cloth to remove large particles of oil and stains on the surface of the industrial filter cloth; the surface washing time is 22 minutes.
[0123] (2) Preparation of sludge solution:
[0124] Add the activated sludge to the salt solution, stir at a speed of 500r / min for 40min, then keep the heat preservation and stand for 4.5 hours at 31°C, filter, remove large particles of solid impurities, and obtain the filtrate as sludge liquid; the activated sludge and salt The solution mixing mass ratio is 120g:1000mL. The salt solution is sodium lauryl sulfate solution; the mass fraction of sodium lauryl sulfate solution is 1.2%.
[0125] (3) Sludge liquid treatment:
[0126] Add the washed industrial filter cloth in step (1) to the sludge ...
PUM
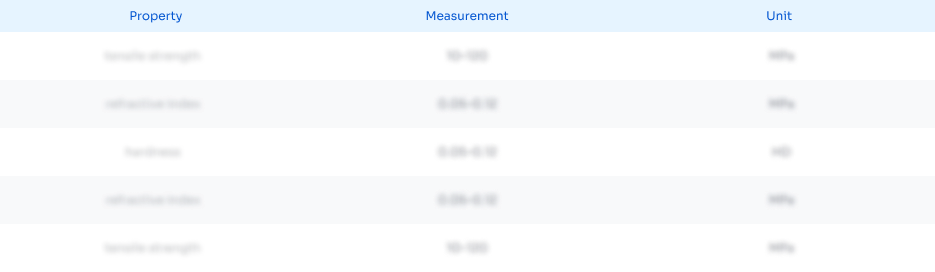
Abstract
Description
Claims
Application Information

- R&D
- Intellectual Property
- Life Sciences
- Materials
- Tech Scout
- Unparalleled Data Quality
- Higher Quality Content
- 60% Fewer Hallucinations
Browse by: Latest US Patents, China's latest patents, Technical Efficacy Thesaurus, Application Domain, Technology Topic, Popular Technical Reports.
© 2025 PatSnap. All rights reserved.Legal|Privacy policy|Modern Slavery Act Transparency Statement|Sitemap|About US| Contact US: help@patsnap.com