Continuous synthesis process of epoxy chloropropane by hydrogen peroxide method
A technology for the synthesis of epichlorohydrin, applied in the direction of organic chemistry, etc., can solve the problems of short catalyst service time, high energy consumption of methanol recovery, complicated process, etc., achieve stable oxidant conversion rate, long service life, and simple process equipment Effect
- Summary
- Abstract
- Description
- Claims
- Application Information
AI Technical Summary
Problems solved by technology
Method used
Image
Examples
Embodiment 1
[0026] (1) press figure 1 Fill the reactor with TS-1 catalyst, fill sections I-III, and install the reactor, pump in deionized water to fill the entire loop reactor, turn on the circulating water bath, the water temperature is 0°C, and turn on the forced circulation pump. Continue to inject deionized water into the system through the metering pump for 4 hours to wash and wet the catalyst, and drain the deionized water; continue to inject methanol into the system through the metering pump for 4 hours to wet and activate the catalyst, and drain the methanol.
[0027] (2) Allyl chloride and methanol are mixed uniformly according to the molar ratio of 1:1;
[0028] (3) Simultaneously turn on metering pumps A and B to feed materials to the mixer, control the molar ratio of chloropropene and hydrogen peroxide to 1:1, and the solubility of hydrogen peroxide is 50 wt%. The residence time of the control material in the loop reactor is 2h;
[0029] (4) Measure the hydrogen peroxide an...
Embodiment 2
[0032] (1) press figure 1 Fill the reactor with TS-1 catalyst, fill the first section, and install the reactor, pump in deionized water to fill the entire loop reactor, turn on the circulating water bath, the water temperature is 10°C, and turn on the forced circulation pump. Continue to inject deionized water into the system for 6 hours to wash and wet the catalyst through the metering pump, and drain the deionized water; continue to inject methanol into the system through the metering pump for 8 hours to moisten and activate the catalyst, and drain the methanol.
[0033] (2) allyl chloride and methanol are mixed evenly according to the molar ratio of 2:1;
[0034] (3) Simultaneously turn on metering pumps A and B to feed materials to the mixer, control the molar ratio of chloropropene and hydrogen peroxide to 1:1, and the solubility of hydrogen peroxide to 10wt%. The residence time of the control material in the loop reactor is 1h;
[0035] (4) with embodiment 1.
[0036]...
Embodiment 3
[0038] (1) press figure 1 Fill the reactor with TS-1 catalyst, fill sections I-IV, and install the reactor, pump in deionized water to fill the entire loop reactor, turn on the circulating water bath, the water temperature is 30°C, and turn on the forced circulation pump. Continue to inject deionized water into the system for 8 hours to wash and wet the catalyst through the metering pump, and drain the deionized water; continue to inject methanol into the system for 6 hours to wet the activated catalyst through the metering pump, and drain the methanol.
[0039] (2) Allyl chloride and methanol are mixed uniformly according to the molar ratio of 1:1;
[0040] (3) Simultaneously turn on the metering pumps A and B to feed the mixer, control the molar ratio of chloropropene and hydrogen peroxide to 3:1, and the solubility of hydrogen peroxide is 70wt%. The residence time of the control material in the loop reactor is 0.1h;
[0041] (4) with embodiment 1.
[0042] (5) with embod...
PUM
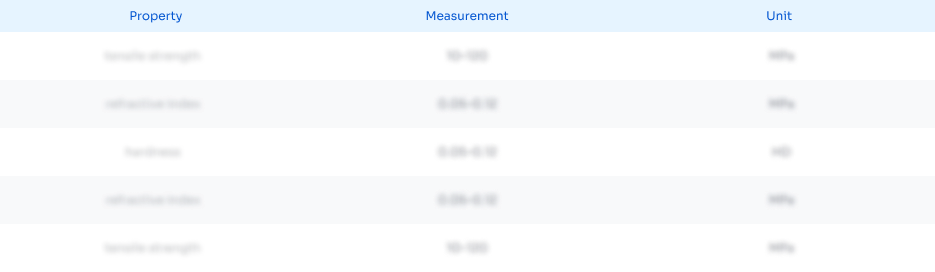
Abstract
Description
Claims
Application Information

- Generate Ideas
- Intellectual Property
- Life Sciences
- Materials
- Tech Scout
- Unparalleled Data Quality
- Higher Quality Content
- 60% Fewer Hallucinations
Browse by: Latest US Patents, China's latest patents, Technical Efficacy Thesaurus, Application Domain, Technology Topic, Popular Technical Reports.
© 2025 PatSnap. All rights reserved.Legal|Privacy policy|Modern Slavery Act Transparency Statement|Sitemap|About US| Contact US: help@patsnap.com