Medium-carbon niobium-vanadium microalloying high-speed wheel steel and wheel preparation method
A niobium-vanadium micro-alloy and wheel steel technology, which is applied in the manufacture of tools, heat treatment equipment, furnace types, etc., can solve the problems of poor adaptability, low strength and hardness, etc., achieve improved wear performance, increased hardness level, and improved material properties Effect
- Summary
- Abstract
- Description
- Claims
- Application Information
AI Technical Summary
Problems solved by technology
Method used
Image
Examples
preparation example Construction
[0041] A method for preparing a medium-carbon niobium-vanadium micro-alloyed high-speed wheel steel using the above-mentioned medium-carbon niobium-vanadium micro-alloyed high-speed wheel steel, including a heat treatment process, and the heat treatment process includes the following steps:
[0042] S1: The wheel is kept warm for 2.0-3.5 hours at a temperature of 850-880°C; the main reason is that Nb and V elements are added. In order to fully exert the effects of Nb and V, it is necessary to increase the heating temperature so that the second phase particles formed are solid-dissolved in the in austenite. When the content of Nb and V is lower than the line, the temperature is 850°C. With the increase of Nb and V content, the temperature increases, but when the temperature exceeds 880°C, the austenite grains will grow significantly. Therefore, the heat treatment temperature is designed at 850-880°C;
[0043] S2: Spray water to cool the wheels after heat preservation; specific...
Embodiment 1
[0047] A medium-carbon niobium-vanadium microalloyed high-speed wheel steel, including the following components in weight percentage: C: 0.52%, Si: 0.25%, Mn: 0.65%, P: 0.003%, S: 0.005%, Nb: 0.01%, V: 0.20%, and the rest are Fe and unavoidable impurity elements. The preparation method of the wheel is as follows: the molten steel containing the above components is passed through the electric furnace steelmaking process, the LF furnace refining process, the RH vacuum treatment process, and the round billet continuous process. Casting process, ingot cutting and rolling process, heat treatment process, processing process, and finished product inspection process. The heat treatment process is: firstly, heat at 860 ° C, keep warm after heating, and after 2.5 hours of heat preservation, the wheels are sprayed with water to cool down. The inner metal of the wheel is cooled to below 550°C at a cooling rate of 2°C / s-5°C / s, and finally tempered at 500°C for 4.5 hours. As a comparative e...
Embodiment 2
[0051] A medium-carbon niobium-vanadium microalloyed high-speed wheel steel, including the following components in weight percentage: C: 0.54%, Si: 0.30%, Mn: 0.65%, P: 0.003%, S: 0.006%, Nb: 0.02%, V: 0.15%, and the rest are Fe and unavoidable impurity elements. The preparation method of the wheel is as follows: the molten steel containing the above components is passed through the electric furnace steelmaking process, the LF furnace refining process, the RH vacuum treatment process, and the round billet continuous process. It is formed by casting process, ingot cutting and rolling process, heat treatment process, processing process and finished product testing process. The heat treatment process is as follows: first heat at 870°C, heat it after heating, keep it warm for 3.0 hours, spray the wheel with water to cool it, and accelerate the cooling of the metal inside the wheel to 550°C at a cooling rate of 2°C / s-5°C / s Thereafter, a final tempering treatment was performed at 50...
PUM
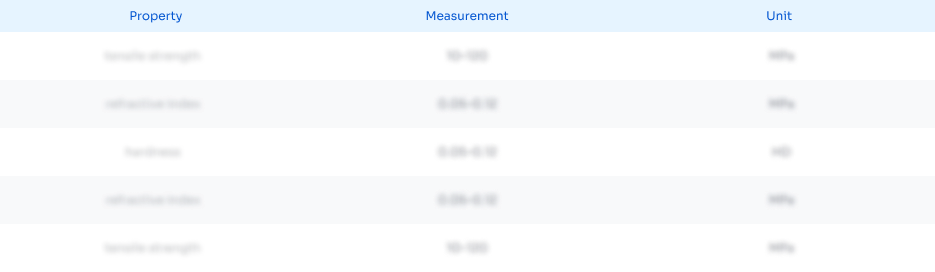
Abstract
Description
Claims
Application Information

- R&D Engineer
- R&D Manager
- IP Professional
- Industry Leading Data Capabilities
- Powerful AI technology
- Patent DNA Extraction
Browse by: Latest US Patents, China's latest patents, Technical Efficacy Thesaurus, Application Domain, Technology Topic, Popular Technical Reports.
© 2024 PatSnap. All rights reserved.Legal|Privacy policy|Modern Slavery Act Transparency Statement|Sitemap|About US| Contact US: help@patsnap.com