Method for removing impurity iron in magnesium alloy by using al-zr master alloy
A technology of master alloy and magnesium alloy, which is applied in the field of removing impurity iron in magnesium alloy by using Al-Zr master alloy to achieve the effect of stable effect
- Summary
- Abstract
- Description
- Claims
- Application Information
AI Technical Summary
Problems solved by technology
Method used
Image
Examples
Embodiment 1
[0020] The original grade of AZ91D magnesium alloy die-casting scrap and returned material is 3.2kg in total, and the average content of impurity Fe in the alloy is 0.015% (mass fraction, the same below). Al-5Zr master alloy, its Zr element content is 5.2%, impurity Fe content is 0.05%.
[0021] The above magnesium alloy was placed in a graphite clay crucible and heated and melted in a resistance crucible furnace.
[0022] The temperature of the magnesium alloy melt is 740°C, and 58g of the Al-5Zr master alloy is added according to the content of the Zr element being 6 times that of the impurity Fe. After the master alloy is melted, argon gas is introduced for refining. After the refining is completed, the 750°C alloy melt is poured into a graphite mold through a 20ppi SiC filter preheated at 750°C.
[0023] Chemical composition analysis The magnesium alloy after Fe removal has an impurity Fe content of 0.0031%, and a residual Zr content of less than 0.001%.
[0024] The imp...
Embodiment 2
[0026] The original brand is AZ31 magnesium alloy die-casting scraps and recycled materials totaling 2kg, and the average content of impurity Fe in the alloy is 0.011%. Al-3Zr master alloy, its Zr element content is 3.1%, impurity Fe content is 0.01%.
[0027] The above magnesium alloy was placed in a graphite clay crucible and heated and melted in a resistance crucible furnace.
[0028] The temperature of the magnesium alloy melt is 680°C, and 36g of the Al-3Zr master alloy is added according to the content of the Zr element being 5 times that of the impurity Fe. After the master alloy is melted, argon gas is introduced for refining. After refining, the 650°C alloy melt is poured into a graphite mold through a 15ppi SiC filter preheated at 760°C.
[0029] Chemical composition analysis of the magnesium alloy after Fe removal has an impurity Fe content of 0.002%.
Embodiment 3
[0031] The original brand is AZ91 magnesium alloy die-casting scrap and returned charge total 2.2kg, the average content of impurity Fe in the alloy is 0.021%. The Al-20Zr master alloy has a Zr element content of 19.8% and an impurity Fe content of 0.02%.
[0032] The above-mentioned magnesium alloy is heated and melted in a magnesia crucible in a medium-frequency induction heating furnace.
[0033] The magnesium alloy melt temperature is 780°C, and 24g of Al-3Zr master alloy is added according to the content of Zr element 10 times that of impurity Fe. After the master alloy is melted, argon gas is introduced for refining. After refining, the 800°C alloy melt is poured into a graphite mold through a 50ppi SiC filter.
[0034] Chemical composition analysis of the magnesium alloy after Fe removal shows that the impurity Fe content is 0.0033%, and the residual Zr content is less than 0.001%.
PUM
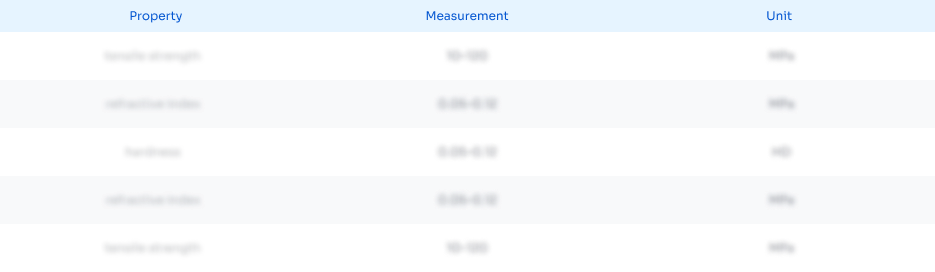
Abstract
Description
Claims
Application Information

- Generate Ideas
- Intellectual Property
- Life Sciences
- Materials
- Tech Scout
- Unparalleled Data Quality
- Higher Quality Content
- 60% Fewer Hallucinations
Browse by: Latest US Patents, China's latest patents, Technical Efficacy Thesaurus, Application Domain, Technology Topic, Popular Technical Reports.
© 2025 PatSnap. All rights reserved.Legal|Privacy policy|Modern Slavery Act Transparency Statement|Sitemap|About US| Contact US: help@patsnap.com