Tar residue resource utilization process
A technology for tar residue and resource utilization is applied in the field of tar residue resource utilization technology to achieve the effect of reducing use and increasing added value
- Summary
- Abstract
- Description
- Claims
- Application Information
AI Technical Summary
Problems solved by technology
Method used
Image
Examples
Embodiment 1
[0026] The raw material characteristics of tar slag are as shown in table 1 in this example:
[0027] Table 1 Raw material characteristics of tar residue
[0028]
[0029] As shown in Table 1, the present invention provides a tar residue resource utilization process of the present invention, which includes the following steps:
[0030] (1) The dusty gas water is cooled and flashed and sent to the tar separator. The tar separator uses the different densities of the components in the dusty gas water to separate tar residue, tar, and water into three different substances; tar and water pass through the tar The upper part of the separator is separated, and the tar residue remains at the bottom of the cone of the tar separator;
[0031] (2) The tar slag is sent to the three-phase centrifuge through the delivery pump at the 1.5-meter opening of the cone bottom of the tar separator, and part of it is transported back to the circular material slag at the cone bottom, and the large...
Embodiment 2
[0046] Step (1) in embodiment two is exactly the same as embodiment one, and the characteristics of tar residue are as shown in table 5:
[0047] Table 5 Raw material characteristics of tar residue
[0048] components Wt% components Wt% fixed carbon 36.6 Oil 9.8 moisture 14.1 Sulfur content 0.24 Ash 11.8 Volatile matter 37.5
[0049] (2) The tar slag is sent to the three-phase centrifuge through the delivery pump at the 1.5-meter opening of the cone bottom of the tar separator, and part of it is transported back to the circular material slag at the cone bottom, and the large particle dust settled at the cone bottom is continuously discharged. Rinse and dilute so that the tar residue at the bottom is evenly mixed, and the tar residue is sent into a three-phase centrifuge to obtain tar, separated water, and solid residue after separation; the parameters of the three-phase centrifuge are shown in Table 6, and the three-phase centrifu...
PUM
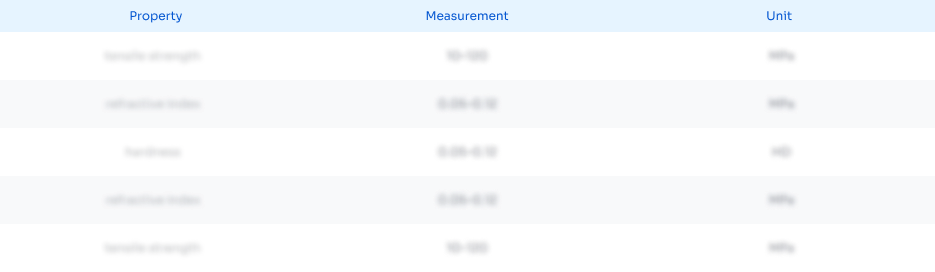
Abstract
Description
Claims
Application Information

- R&D
- Intellectual Property
- Life Sciences
- Materials
- Tech Scout
- Unparalleled Data Quality
- Higher Quality Content
- 60% Fewer Hallucinations
Browse by: Latest US Patents, China's latest patents, Technical Efficacy Thesaurus, Application Domain, Technology Topic, Popular Technical Reports.
© 2025 PatSnap. All rights reserved.Legal|Privacy policy|Modern Slavery Act Transparency Statement|Sitemap|About US| Contact US: help@patsnap.com