Stamping assembly type guardrail and assembling equipment thereof
An assembly equipment and assembly technology, applied in the direction of fences, building types, non-rotational vibration suppression, etc., can solve the problems of welding guardrail processing troubles, high maintenance costs, low labor efficiency, etc., to avoid Faraday shielding effect, installation Convenient and fast, stable and reliable installation
- Summary
- Abstract
- Description
- Claims
- Application Information
AI Technical Summary
Problems solved by technology
Method used
Image
Examples
Embodiment Construction
[0025] The specific embodiment of the present invention is described in further detail below in conjunction with accompanying drawing:
[0026] refer to Figure 4 As shown, in the prior art, the crossbeam is pre-drilled, and a plurality of insertion holes are opened on the crossbeam. After the crossbeam is placed on a platform, a single longitudinal beam is manually inserted into the insertion hole for assembly. After assembly, welding is carried out at the X position in the figure, so that the beam and the longitudinal beam are firmly connected to form a guardrail. Since the difference between the peripheral size of the longitudinal beam and the size of the insertion hole is very small (up to about 0.5mm), the insertion is very easy. Inconvenient, low labor efficiency and high labor intensity, and the welding is prone to Faraday effect, rust and reduce the service life of the product.
[0027] as attached figure 1 and figure 2 As shown, the embodiment of the stamped assem...
PUM
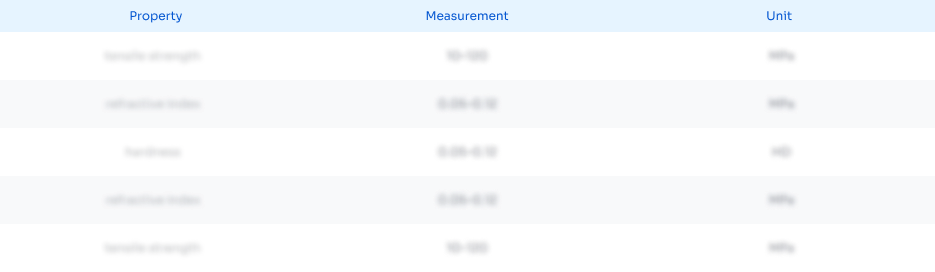
Abstract
Description
Claims
Application Information

- R&D
- Intellectual Property
- Life Sciences
- Materials
- Tech Scout
- Unparalleled Data Quality
- Higher Quality Content
- 60% Fewer Hallucinations
Browse by: Latest US Patents, China's latest patents, Technical Efficacy Thesaurus, Application Domain, Technology Topic, Popular Technical Reports.
© 2025 PatSnap. All rights reserved.Legal|Privacy policy|Modern Slavery Act Transparency Statement|Sitemap|About US| Contact US: help@patsnap.com