High-strength fiber cement composite board and preparation method thereof
A cement composite board and high-strength fiber technology, which is applied in the field of building materials engineering, can solve the problems of loss of inorganic materials, reaction imbalance, and low lateral strength, etc., and achieve enhanced anti-permeability, high water solubility, and low porosity. Effect
- Summary
- Abstract
- Description
- Claims
- Application Information
AI Technical Summary
Problems solved by technology
Method used
Examples
Embodiment approach
[0037] According to an embodiment of the present invention, before mixing materials, natural water is passed through a quantum processor, and quantum energy is implanted in the water, which resonates with water at a harmonic frequency to cut water molecular chains and hydrogen chains to make macromolecular clusters water It becomes water with small molecular clusters, implanting water with quantum energy to obtain greater free energy than common water, using treated water as mixing material water, and mixing with various raw materials according to the designed production process to form cement slurry that is Can.
[0038] In one embodiment of the present invention, the present invention adopts a separate mixing process, and the cement slurry is prepared first with a high-speed mixing tank. After the slurry is fully mixed in the high-speed mixing tank, the slurry is mixed with the plant fiber in a rolling mill. . When the well-mixed cement slurry is in contact with the plant f...
PUM
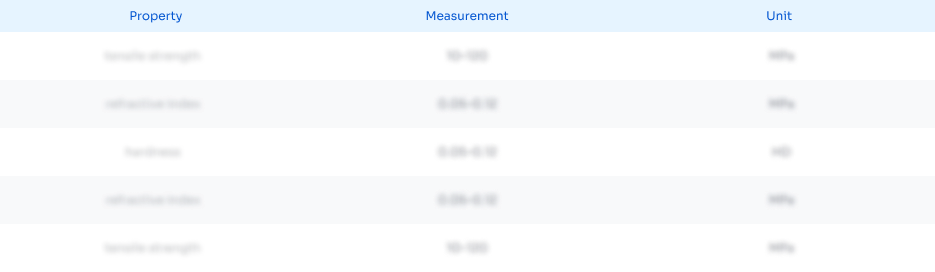
Abstract
Description
Claims
Application Information

- R&D Engineer
- R&D Manager
- IP Professional
- Industry Leading Data Capabilities
- Powerful AI technology
- Patent DNA Extraction
Browse by: Latest US Patents, China's latest patents, Technical Efficacy Thesaurus, Application Domain, Technology Topic, Popular Technical Reports.
© 2024 PatSnap. All rights reserved.Legal|Privacy policy|Modern Slavery Act Transparency Statement|Sitemap|About US| Contact US: help@patsnap.com