A composite film for liquid medicine packaging and its dry composite process
A technology of dry lamination and dry lamination machine, which is applied in the field of liquid pharmaceutical packaging lamination film and its dry lamination process, which can solve the problems of affecting the bonding force of the lamination film, incomplete removal of solvent, and increase of solvent residue, etc., to achieve production efficiency Improve and reduce the effect of solvent surface skinning and increase solvent volatilization speed
- Summary
- Abstract
- Description
- Claims
- Application Information
AI Technical Summary
Problems solved by technology
Method used
Image
Examples
Embodiment 1
[0069] Adopt the technology of the present invention to prepare PET-AL-CPP, and the technological process is as follows figure 1 shown, including the following specific steps:
[0070] 1. Printing:
[0071] Turn on the printing machine, place the corona-treated PET substrate on the inner layer in the unwinding section of the gravure printing machine, control the unwinding tension to 100N, and then enter the printing section, control the speed of the printing machine to 130m / min, and control the drying temperature at 60℃, control the printing roller pressure to 0.2Mpa and the printing blade pressure to 0.2Mpa, and print the outer layer of the PET substrate. Before printing, use ethyl acetate to adjust the ink viscosity to 13S. After printing, control the winding tension to 60N for winding. .
[0072] 2. Aluminum foil composite:
[0073] Transfer the PET base material printed on the outer layer to the unwinding part of the dry laminating machine, control the unwinding tension...
Embodiment 2
[0079] Example 2
[0080] It is investigated that the temperature of the drying tunnel and the compounding speed are both at the upper limit, that is, the temperature of the first drying tunnel 1 is 72-75 °C; the temperature of the second drying tunnel 2 is 78-80 °C, and the temperature of the third drying tunnel 3 is 88-90 ℃, when the compounding speed is also at the upper limit, that is, the compounding speed of PET and AL is adjusted to 150m / min, and the compounding speed of PET-AL and CPP is adjusted to 200m / min, the performance of the compound film.
Embodiment 3
[0082] Compared with Example 2, the third gear 7 is removed, so that the power drive of the flow aid guide roller 11 to the flow aid 4 is released, that is, the flow aid stops working, and the PET-AL-CPP composite film is obtained.
PUM
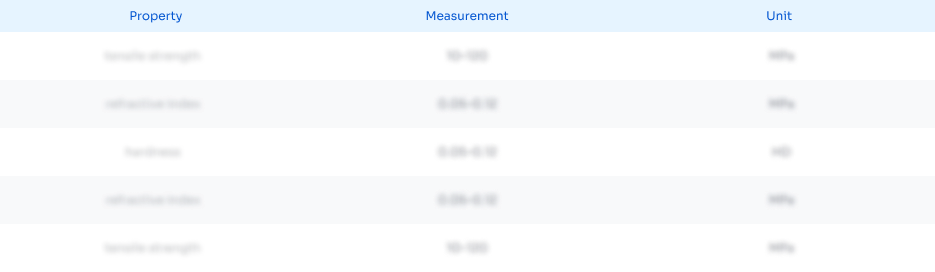
Abstract
Description
Claims
Application Information

- R&D Engineer
- R&D Manager
- IP Professional
- Industry Leading Data Capabilities
- Powerful AI technology
- Patent DNA Extraction
Browse by: Latest US Patents, China's latest patents, Technical Efficacy Thesaurus, Application Domain, Technology Topic, Popular Technical Reports.
© 2024 PatSnap. All rights reserved.Legal|Privacy policy|Modern Slavery Act Transparency Statement|Sitemap|About US| Contact US: help@patsnap.com