Durability testing system and method for hydraulic control unit in automobile braking system
An automotive braking system and control unit technology, applied in vehicle testing, machine/structural component testing, measuring devices, etc., can solve problems affecting the stability of HCU use, and achieve improved efficiency and consistency of braking characteristics stable effect
- Summary
- Abstract
- Description
- Claims
- Application Information
AI Technical Summary
Problems solved by technology
Method used
Image
Examples
Embodiment 1
[0041] Such as figure 1 As shown, the embodiment of the present invention provides a durability test system for a hydraulic control unit in an automobile braking system, including: an air pressure supply system, an air pressure pipeline system, a measurement and control system, and an environment simulation system.
[0042] The air pressure supply system includes an air source 1 , a two-position five-way solenoid valve 2 and a cylinder 3 connected in sequence through pipelines.
[0043]The pneumatic pipeline system includes an oil pot 4, a fuel tank 5, a master cylinder 6, a pneumatic ball valve 7-14, a pressure sensor 15-20 and a simulated wheel cylinder 21-24, and the cylinder 3 is connected to the master cylinder 6 by pushing; The overflow port of the oil pot 4 is connected with the oil tank 5 through the return line 34, the oil outlet of the oil pot 4 is connected with the oil inlet of the master cylinder 6, and the two outlets of the master cylinder 6 The oil ports are r...
Embodiment 2
[0098] Such as figure 2 As shown, the embodiment of the present invention provides a method for testing the durability of a hydraulic control unit in an automobile braking system, including:
[0099] Step 1, the control environment simulation system changes the ambient temperature where the hydraulic control unit is located to reach a preset value;
[0100] Step 2, control the air source to push the master cylinder to make its pressure reach the preset value;
[0101] Step 3, according to the test sample, control the state of each solenoid valve and motor in the hydraulic control unit, and perform a durability test on it;
[0102] Step 4, collecting the pressure sensor signals on the two inlet pipelines of the hydraulic control unit and the pressure sensor signals on the pipelines where the four simulated wheel cylinders are located;
[0103] Step 5, repeat the above steps 1 to 4 to complete the durability test of the hydraulic control unit under different combinations of m...
PUM
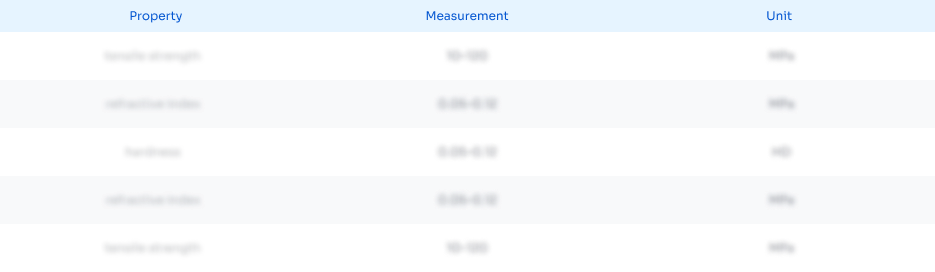
Abstract
Description
Claims
Application Information

- R&D Engineer
- R&D Manager
- IP Professional
- Industry Leading Data Capabilities
- Powerful AI technology
- Patent DNA Extraction
Browse by: Latest US Patents, China's latest patents, Technical Efficacy Thesaurus, Application Domain, Technology Topic, Popular Technical Reports.
© 2024 PatSnap. All rights reserved.Legal|Privacy policy|Modern Slavery Act Transparency Statement|Sitemap|About US| Contact US: help@patsnap.com