Hollow-structure rubber and fabric composite sealing element and forming method thereof
A technology of compound sealing and molding method, applied in the direction of engine sealing, engine components, mechanical equipment, etc., can solve problems such as the inability to take out the mold core, the eccentricity of the seal product, and the change of the internal shape of the product, so as to achieve good appearance quality and uniform size. , The effect of simplifying the mold installation process
- Summary
- Abstract
- Description
- Claims
- Application Information
AI Technical Summary
Problems solved by technology
Method used
Image
Examples
Embodiment Construction
[0042] In order to make the object, technical solution and advantages of the present invention clearer, the present invention will be further described in detail below in conjunction with the accompanying embodiments. Obviously, the described embodiments are only some embodiments of the present invention, rather than all embodiments. Based on the embodiments of the present invention, all other embodiments obtained by persons of ordinary skill in the art without making creative efforts belong to the protection scope of the present invention.
[0043] see figure 1 and figure 2 , the present invention proposes a hollow structure rubber and fabric composite seal, the material of the main body of the composite seal is silicone rubber, and a layer of reinforcing fabric is integrally covered on the surface of the silicone rubber, the seal includes a hollow structure main body, a hollow structure Both sides of the bottom of the main body are planar structures, and the seals are conn...
PUM
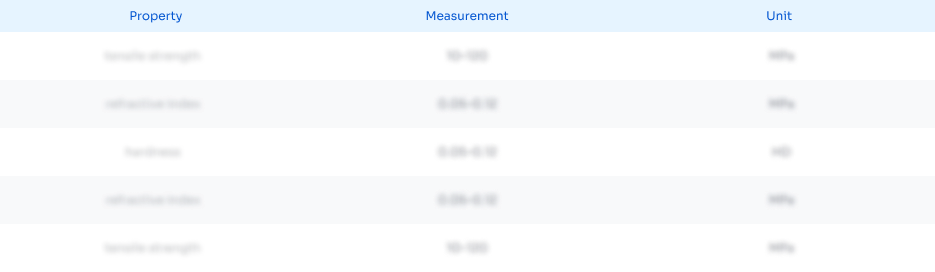
Abstract
Description
Claims
Application Information

- Generate Ideas
- Intellectual Property
- Life Sciences
- Materials
- Tech Scout
- Unparalleled Data Quality
- Higher Quality Content
- 60% Fewer Hallucinations
Browse by: Latest US Patents, China's latest patents, Technical Efficacy Thesaurus, Application Domain, Technology Topic, Popular Technical Reports.
© 2025 PatSnap. All rights reserved.Legal|Privacy policy|Modern Slavery Act Transparency Statement|Sitemap|About US| Contact US: help@patsnap.com