High-flux characterization method for wear resistance of composite material
A composite material and wear resistance technology, applied in the field of powder metallurgy, can solve the problem of wasting equipment and machine time, and achieve the effect of ensuring accuracy and shortening the research and development cycle.
- Summary
- Abstract
- Description
- Claims
- Application Information
AI Technical Summary
Problems solved by technology
Method used
Image
Examples
Embodiment Construction
[0021] (1) A high-throughput characterization method for the wear resistance of composite materials is used to study the effect of graphite volume fraction on the wear resistance of Cu / C composites
[0022] First divide the cylindrical mold into 14 equal parts with the separator, and the graphite content in each part of the composite blank is 5vol%~70vol%, and the interval is 5vol%. After a little compaction, the separator is drawn out, and the cold pressing-sintering -Preparation of dense Cu / C composite discs by recompression-refiring method. According to the following parameters, the disc is processed into the shape of an involute standard straight-edge cylindrical gear: the standard modulus is selected as 2.5, the number of teeth is 42, that is, each partition occupies 3 teeth, the diameter of the index circle is 105mm; the tooth width coefficient is 0.3, The tooth width is 31.5mm; the tooth top height coefficient is 1, and the top clearance coefficient is 0.25. The grindi...
PUM
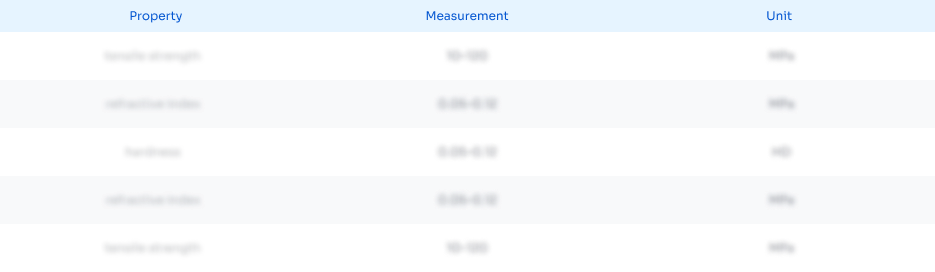
Abstract
Description
Claims
Application Information

- R&D Engineer
- R&D Manager
- IP Professional
- Industry Leading Data Capabilities
- Powerful AI technology
- Patent DNA Extraction
Browse by: Latest US Patents, China's latest patents, Technical Efficacy Thesaurus, Application Domain, Technology Topic, Popular Technical Reports.
© 2024 PatSnap. All rights reserved.Legal|Privacy policy|Modern Slavery Act Transparency Statement|Sitemap|About US| Contact US: help@patsnap.com