Microgripper with two-stage constant force output in continuous two strokes and control method
A micro-clamp, constant force technology, applied in the field of micro-manipulation, can solve the problems of difficulty in meeting the operation requirements of small batches and multi-size micro-assembly objects, complex control, and difficulty in adapting to multi-size micro-manipulation objects.
- Summary
- Abstract
- Description
- Claims
- Application Information
AI Technical Summary
Problems solved by technology
Method used
Image
Examples
Embodiment Construction
[0025] In order to make the purpose, technical solution and important research significance of the present invention more clear, the specific implementation of the present invention will be described in detail below in conjunction with the accompanying drawings. Based on the embodiments of the present invention, all embodiments obtained by persons of ordinary skill in the art without making creative efforts belong to the protection scope of the present invention.
[0026] Such as figure 1 , 2 As shown, the continuous two-stroke two-stage constant-force micro gripper is composed of jaws (1), shuttle bar a (2), bistable beam D (3), bistable beam C (4), base part ( 5), the integrated compliant micro-clamp composed of the lever part (6), the shuttle bar b (7), the bistable beam B (8) and the bistable beam A (9).
[0027] The realization of the two-level constant force is based on the negative stiffness effect (stress stiffening effect) of the bistable beam, that is, when there i...
PUM
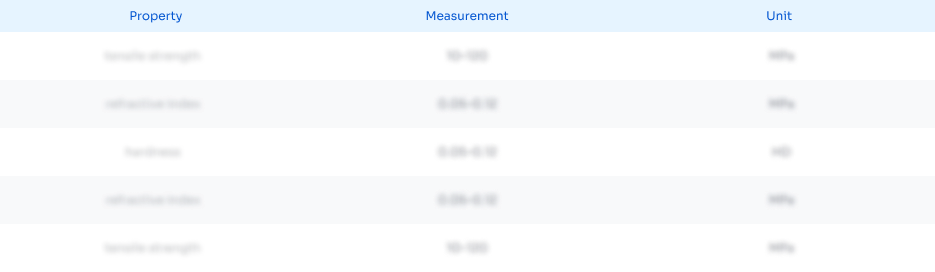
Abstract
Description
Claims
Application Information

- Generate Ideas
- Intellectual Property
- Life Sciences
- Materials
- Tech Scout
- Unparalleled Data Quality
- Higher Quality Content
- 60% Fewer Hallucinations
Browse by: Latest US Patents, China's latest patents, Technical Efficacy Thesaurus, Application Domain, Technology Topic, Popular Technical Reports.
© 2025 PatSnap. All rights reserved.Legal|Privacy policy|Modern Slavery Act Transparency Statement|Sitemap|About US| Contact US: help@patsnap.com