Step tubular beam welding fixture
A technology for welding tooling and pipe beams, applied in welding equipment, auxiliary welding equipment, welding/cutting auxiliary equipment, etc., can solve the problems that welding accuracy cannot be effectively guaranteed, lack of welding tooling, and high welding accuracy requirements
- Summary
- Abstract
- Description
- Claims
- Application Information
AI Technical Summary
Problems solved by technology
Method used
Image
Examples
Embodiment
[0017] Such as Figure 1-3 As shown, a step tube beam welding tool, such as figure 1 As shown, the stepping pipe beam 10 includes an "S"-shaped pipe body 11 and a plurality of brackets 13 arranged sequentially along the front end to the rear end of the pipe body 11. The front end of the pipe body 11 is also connected to a flange 12, as figure 2 As shown, the welding tool 20 includes a base 21, and the base 21 is provided with a front end pipe support 22, a middle pipe support 26 and a rear end corresponding to the front end, the front end near the middle, and the rear end of the pipe body 11, respectively. The pipe body support 27, the height of the front end pipe body support 22 and the middle pipe body support 26 is consistent, and the rear end pipe body support 27 is lower than the front end pipe body support 22 and the middle pipe body support 26, The front-end pipe body support 22 is provided with a rectangular slot 25 cooperating with the side of the flange 12, and the...
PUM
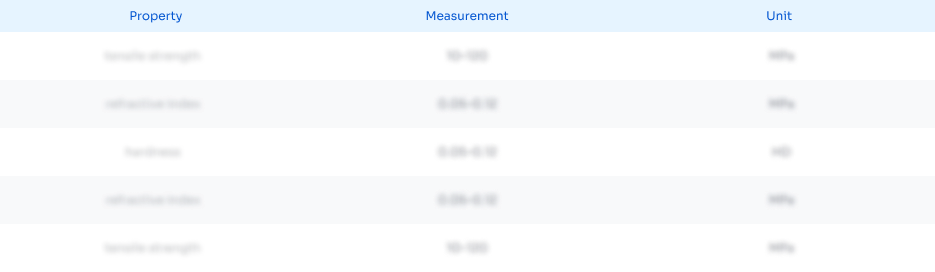
Abstract
Description
Claims
Application Information

- Generate Ideas
- Intellectual Property
- Life Sciences
- Materials
- Tech Scout
- Unparalleled Data Quality
- Higher Quality Content
- 60% Fewer Hallucinations
Browse by: Latest US Patents, China's latest patents, Technical Efficacy Thesaurus, Application Domain, Technology Topic, Popular Technical Reports.
© 2025 PatSnap. All rights reserved.Legal|Privacy policy|Modern Slavery Act Transparency Statement|Sitemap|About US| Contact US: help@patsnap.com