Manufacturing method of nano shell powder plastic ingot
A production method and technology of shell powder, which is applied in the field of production of nano-shell powder plastic ingots, can solve the problems of wasting antistatic and anti-ultraviolet effects of oyster shells, and achieve the effect of expanding the scope of application
- Summary
- Abstract
- Description
- Claims
- Application Information
AI Technical Summary
Problems solved by technology
Method used
Image
Examples
Embodiment Construction
[0027] In order to have a further understanding of the present invention, the following examples are listed for illustration.
[0028] The present invention mainly provides a method for making a nano-shell powder plastic ingot, wherein the making of the nano-shell powder plastic ingot 1 at least includes: firstly selecting a shell 11 suitable for production, cleaning the surface of the shell 11 until it is clean, and then, The shell 11 is dried B, the shell 11 is calcined into shell ash 12 after drying, the shell ash 12 is ground C into nano-shell powder 13, and then, at least one layer of dispersant layer is wrapped on the surface of the nano-shell powder 13 2, and the nano-shell powder 13 is wrapped with at least one layer of graft copolymer layer 3 outside the dispersant layer 2, and the surface of the graft copolymer layer 3 is distributed with protruding grafts 31, and then, the nano-shell powder 13 Put at least one plastic 4 into at least one plastic ingot making machine...
PUM
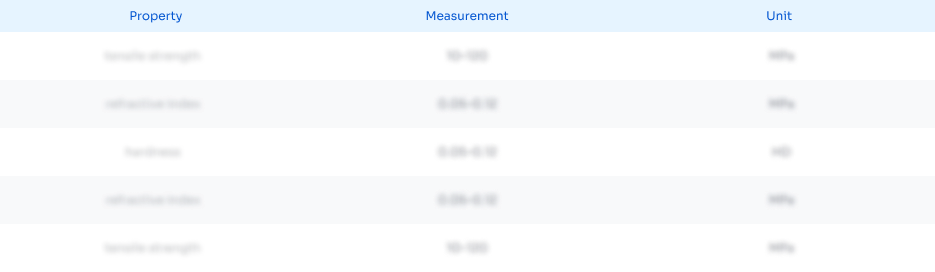
Abstract
Description
Claims
Application Information

- R&D
- Intellectual Property
- Life Sciences
- Materials
- Tech Scout
- Unparalleled Data Quality
- Higher Quality Content
- 60% Fewer Hallucinations
Browse by: Latest US Patents, China's latest patents, Technical Efficacy Thesaurus, Application Domain, Technology Topic, Popular Technical Reports.
© 2025 PatSnap. All rights reserved.Legal|Privacy policy|Modern Slavery Act Transparency Statement|Sitemap|About US| Contact US: help@patsnap.com