Method for preparing tert-butylamine by taking MTBE as raw material
A technology of tert-butylamine and raw materials, applied in the field of preparation of tert-butylamine, which can solve problems such as environmental pollution, harsh reaction conditions, and strong corrosiveness of catalysts
- Summary
- Abstract
- Description
- Claims
- Application Information
AI Technical Summary
Problems solved by technology
Method used
Image
Examples
preparation example Construction
[0035] The preparation process of solid superacid catalyst: one, 50~100g ZrOCl2 Dissolved in ethanol to obtain ZrOCl with a mass concentration of 30% to 50% 2 Ethanol solution, titrated with 20% to 25% ammonia water until no white precipitate, washed several times with deionized water, 5 to 10 minutes each time, at a washing temperature of 40 to 50 ° C, until there was no chloride ion, and then washed at 80 Place it in a vacuum drying oven at ~90°C for 4-6 hours, extrude it, and then bake it at 500°C for 8 hours to obtain white solid particles for use. 2. Impregnate the white particles obtained in Step 1 with a silver nitrate sulfuric acid solution with a concentration of 2-4mol / L, the impregnation temperature is 55-60°C, and the impregnation time is 4-6h; the decompression vacuum degree is 15000-20000Pa; the ultrasonic vibration frequency is 50 ~60kHz, then dry the solid particles in a vacuum drying oven at 80-90°C for 4-6 hours, and then bake at 500°C for 8 hours to obtain P...
Embodiment 1
[0039] (1) Preparation of solid superacid catalyst: a: 50 grams of ZrOCl 2 Dissolved in ethanol to obtain a mass concentration of 30% ZrOCl 2 Ethanol solution, titrated with 20% ammonia water until there is no white precipitate, washed 5 times with deionized water, 10 minutes each time, washing temperature is 40 ° C, washed to no chloride ion, and then placed in vacuum drying at 90 ° C Dry in an oven for 6 hours, extrude and then bake at 500°C for 8 hours to obtain white solid particles for use. b: impregnate the white particles obtained in step a with a silver nitrate sulfuric acid solution with a concentration of 2mol / L, the impregnation temperature is 55°C, and the impregnation time is 6h; the decompression vacuum degree is 16000Pa; the ultrasonic vibration frequency is 56kHz, and then the solid particles are placed at 90°C Dry it in a vacuum oven for 6 hours under the condition of 500°C for 8 hours to obtain the particle I. c: Repeat the impregnation process of step b wi...
Embodiment 2
[0042] (1) Preparation of solid superacid catalyst: a: 50 grams of ZrOCl 2 Dissolved in ethanol to obtain a mass concentration of 30% ZrOCl 2 Ethanol solution, titrated with 20% ammonia water until there is no white precipitate, washed 5 times with deionized water, 10 minutes each time, washing temperature is 40 ° C, washed to no chloride ion, and then placed in vacuum drying at 90 ° C Dry in an oven for 6 hours, extrude and then bake at 500°C for 8 hours to obtain white solid particles for use. b: impregnate the white particles obtained in step a with a silver nitrate sulfuric acid solution with a concentration of 2mol / L, the impregnation temperature is 55°C, and the impregnation time is 6h; the decompression vacuum degree is 17000Pa; the ultrasonic vibration frequency is 57kHz, and then the solid particles are heated at 90°C Dry it in a vacuum oven for 6 hours under the condition of 500°C for 8 hours to obtain the particle I. c: Repeat the impregnation process of step b wi...
PUM
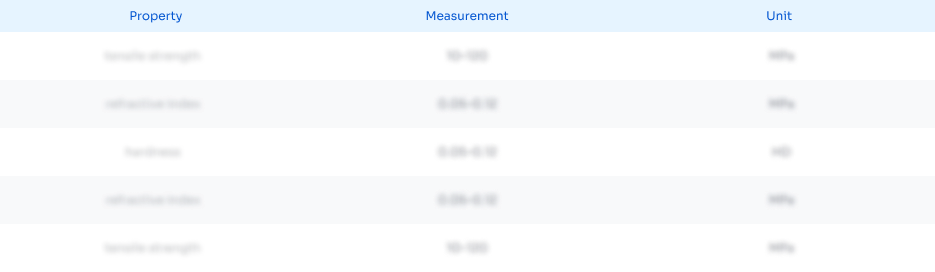
Abstract
Description
Claims
Application Information

- Generate Ideas
- Intellectual Property
- Life Sciences
- Materials
- Tech Scout
- Unparalleled Data Quality
- Higher Quality Content
- 60% Fewer Hallucinations
Browse by: Latest US Patents, China's latest patents, Technical Efficacy Thesaurus, Application Domain, Technology Topic, Popular Technical Reports.
© 2025 PatSnap. All rights reserved.Legal|Privacy policy|Modern Slavery Act Transparency Statement|Sitemap|About US| Contact US: help@patsnap.com