Magnesium-aluminum alloy casting method and magnesium-aluminum alloy casting position adjusting method
A magnesium-aluminum alloy, position adjustment technology, applied in the field of magnesium-aluminum alloy casting position adjustment, magnesium-aluminum alloy casting, can solve the problems of harming magnesium-aluminum alloy, containing bubbles, lack of meat, etc., and achieve the effect of enhancing the sealing ability
- Summary
- Abstract
- Description
- Claims
- Application Information
AI Technical Summary
Problems solved by technology
Method used
Image
Examples
specific Embodiment approach 1
[0069] This embodiment is an embodiment of a magnesium-aluminum alloy die-casting device.
[0070] Such as Figure 1-7 As shown, a magnesium-aluminum alloy die-casting device disclosed in this embodiment includes a clamping member 1 and a die-casting mold 2;
[0071] The clamping member 1 includes an upper support frame 1-1, a support platform 1-2, an upper plate 1-3, an upper template 1-4, an upper connecting rod 1-5, a return spring 1-6, and an upper splint 1- 7. Guide sleeve 1-8, lower support frame 1-9, support platform 1-10, guide rod 1-11, lower splint 1-12 and deflection member 1-13; the lower end of the upper support frame 1-1 is set There is an upper support platform 1-2, the upper and lower end surfaces of the upper support platform 1-2 are sequentially provided with an upper beating plate 1-3 and an upper template 1-4, and a plurality of upper connecting rods 1-5 are arranged, and the upper connecting rods One end of the rod 1-5 passes through the return spring 1-...
specific Embodiment approach 2
[0079] This embodiment is an embodiment of a magnesium-aluminum alloy die-casting device.
[0080] A magnesium-aluminum alloy casting method disclosed in this embodiment includes the following steps:
[0081] Step a, fixed installation, first process the upper support frame 1-1 and the lower support frame 1-9 to be fixed on the machine tool, the upper support frame 1-1 is fixed to the dynamic template part of the machine tool, and the lower support frame 1-9 is fixed to the static part of the punch press For the formwork part, the installation is completed, and then, the bottom plate 2-3 is arranged on the inner bottom end of the two-way opening mold 2-1, and the two-way opening mold 2-1 is installed on the upper end of the lower splint 1-12, through the lower splint 1-12 Set the limit piece to limit and fix, then fix the cover plate 2-2 on the upper end of the two-way opening mold 2-1, and seal the cover. At this time, the upper splint 1-7 and the cover plate 2-2 are in a sep...
specific Embodiment approach 3
[0089] This embodiment is an embodiment of a magnesium-aluminum alloy die-casting device
[0090] It should be noted that the deflection member for magnesium-aluminum alloy die-casting in this embodiment can be implemented alone, that is, it can exist alone as a part of a magnesium-aluminum alloy die-casting device, or it can be used for the one described in the first embodiment. Magnesium-aluminum alloy die-casting devices are further defined.
[0091] combine Figure 1-6 As shown, a deflection member for magnesium-aluminum alloy die-casting disclosed in this embodiment includes a threaded sleeve 1-13-1, a lower connecting rod 1-13-2, a deflection motor 1-13-3, and a worm 1-13- 4. The plurality of threaded sleeves 1-13-1 are arrayed in the rectangular cavity inside the lower support platform 1-10, and the upper and lower ends of the threaded sleeves 1-13-1 are set in the rectangular cavity through bearings. On the upper and lower side walls of the cavity, a plurality of low...
PUM
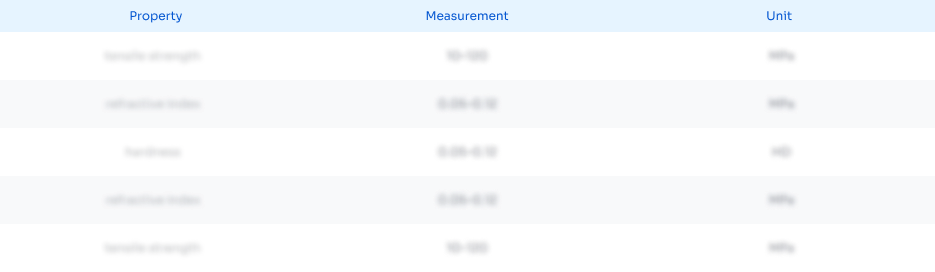
Abstract
Description
Claims
Application Information

- R&D
- Intellectual Property
- Life Sciences
- Materials
- Tech Scout
- Unparalleled Data Quality
- Higher Quality Content
- 60% Fewer Hallucinations
Browse by: Latest US Patents, China's latest patents, Technical Efficacy Thesaurus, Application Domain, Technology Topic, Popular Technical Reports.
© 2025 PatSnap. All rights reserved.Legal|Privacy policy|Modern Slavery Act Transparency Statement|Sitemap|About US| Contact US: help@patsnap.com