Extrusion molding process method of heat-resistant and corrosion-resistant screen
A technology of extrusion molding and process method, which is applied in the field of screen mesh production, can solve the problems of reduced lifespan, achieve the effects of improved strength and toughness, high chlorine content, and fast vulcanization speed
- Summary
- Abstract
- Description
- Claims
- Application Information
AI Technical Summary
Problems solved by technology
Method used
Image
Examples
Embodiment 1
[0023]The heat-resistant and corrosion-resistant screen is made by extruding through a rotating head. The specific extrusion molding process includes the following steps: the first step, the weight ratio of acrylate rubber to chlorinated polyether is 51~56:82~ 93, and based on the total weight of 100 parts by weight of acrylate rubber and chlorinated polyether, the total amount of reinforcing fillers is 20 parts by weight, the total amount of antioxidants is 0.5 parts by weight, and the total amount of plasticizers 8 parts by weight, the acrylic rubber is masticated, and then a reinforcing filler, an anti-aging agent and a plasticizer are added for mixing to obtain an acrylic rubber masterbatch. The masticating time is 15 minutes, and the mixing time is 35 minutes; Two steps, the acrylic ester rubber masterbatch that step one obtains is dispersed in ionic liquid and isobornyl methacrylate to form acrylic ester rubber compound glue, with the total weight of the acrylic ester rub...
Embodiment 2
[0025] The heat-resistant and corrosion-resistant screen is made by extruding through a rotating machine head. The specific extrusion molding process includes the following steps: the first step, the weight ratio of acrylate rubber to chlorinated polyether is 51:82, and The total weight of 100 parts by weight of acrylate rubber and chlorinated polyether is based on the total weight of the reinforcing filler. , the acrylate rubber is masticated, and then adding reinforcing filler, anti-aging agent and plasticizer for mixing to obtain acrylate rubber masterbatch, the masticating time is 3min, and the mixing time is 5min; in the second step, the The acrylate rubber masterbatch obtained in step 1 is dispersed in ionic liquid and isobornyl methacrylate to form acrylate rubber mixture, based on the total weight of 100 parts by weight of acrylate rubber and chlorinated polyether, the ionic liquid The dosage is 30 parts by weight, 12 parts by weight of isobornyl methacrylate; the thir...
PUM
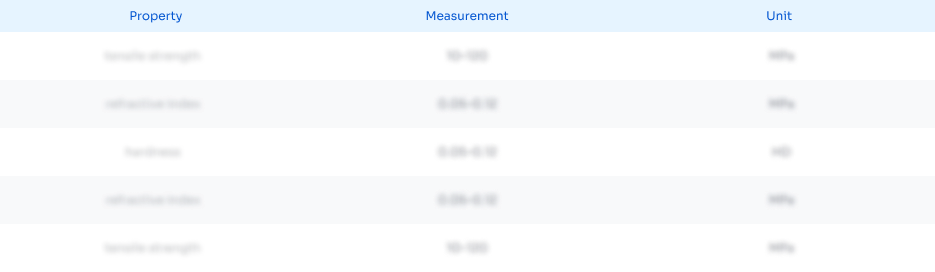
Abstract
Description
Claims
Application Information

- Generate Ideas
- Intellectual Property
- Life Sciences
- Materials
- Tech Scout
- Unparalleled Data Quality
- Higher Quality Content
- 60% Fewer Hallucinations
Browse by: Latest US Patents, China's latest patents, Technical Efficacy Thesaurus, Application Domain, Technology Topic, Popular Technical Reports.
© 2025 PatSnap. All rights reserved.Legal|Privacy policy|Modern Slavery Act Transparency Statement|Sitemap|About US| Contact US: help@patsnap.com