Composite navigation type differential storage robot and working method thereof
A compound navigation and robot technology, applied in the field of compound navigation differential storage robots, can solve the problems of single device function, independence without cooperation, and large application limitations, so as to simplify the conversion of electronic modules, improve stability, and improve stability Effects on Sex and Accuracy
- Summary
- Abstract
- Description
- Claims
- Application Information
AI Technical Summary
Problems solved by technology
Method used
Image
Examples
Embodiment Construction
[0041] Such as Figure 1-6 As shown, the composite navigation differential storage robot is used for the storage workplace where the robot’s working path is marked with a two-dimensional code on the ground. industrial camera 38; when the storage robot travels according to the working path, the industrial control computer obtains the coordinate position data of the robot with the two-dimensional code information read by the industrial camera, and obtains the heading angle after the robot reads the two-dimensional code with the gyroscope sensor assembly Data, and calculate the robot's course angle deviation and course position deviation with the robot coordinate position data and course angle data, and control the robot's driving mechanism according to the calculation results to correct the robot course.
[0042] The gyro sensor assembly includes a nine-axis gyro sensor.
[0043] The warehousing robot uses a knapsack lifting and transferring mechanism to carry the goods in the ...
PUM
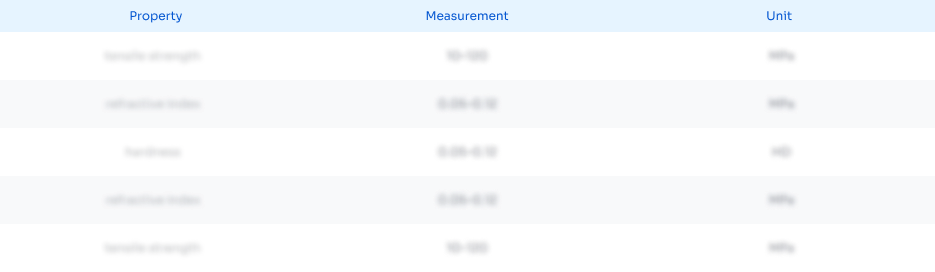
Abstract
Description
Claims
Application Information

- R&D
- Intellectual Property
- Life Sciences
- Materials
- Tech Scout
- Unparalleled Data Quality
- Higher Quality Content
- 60% Fewer Hallucinations
Browse by: Latest US Patents, China's latest patents, Technical Efficacy Thesaurus, Application Domain, Technology Topic, Popular Technical Reports.
© 2025 PatSnap. All rights reserved.Legal|Privacy policy|Modern Slavery Act Transparency Statement|Sitemap|About US| Contact US: help@patsnap.com