Boiler feed water system with turbine exhaust steam recovery
A boiler feed water and steam turbine technology, applied in feed water heaters, preheating, steam generation, etc., can solve the problems of low efficiency of thermal power plants, limited energy saving of steam turbine exhaust multi-stage heat recovery technology, and inability to pump exhaust steam from steam turbines into boilers, etc. question
- Summary
- Abstract
- Description
- Claims
- Application Information
AI Technical Summary
Problems solved by technology
Method used
Image
Examples
Embodiment Construction
[0011] exist figure 1 Among them, the steam-water mixing feedwater assembly 27 flows through the small split pipe 1 through the economizer 33, the evaporative cooler 29, and the feedwater pump 12 (cooled by the evaporative cooler 29, and the water is used as the working medium of the Rankine cycle " The heat that exceeds the "safe working temperature" of the pump 12 is first transferred to the condensation heater 32 in the flow-through section of the pump 12 through the compressor 30 before being allowed to enter the pump 12. The flow water enters the injector inlet 2) of several injectors 15 connected in parallel, the injection overpressure chamber 3, the jet outlet 4, the jet water guide strip steam chamber 26 (the horizontal arrangement of several triangular strips 36 combined along the flow) Gripper 5, flat grate 5 is lapped on the oblique grate 9 clamped by the double flange connection assembly 19), the injection volume is wrapped around the steam port 10, and the swirl t...
PUM
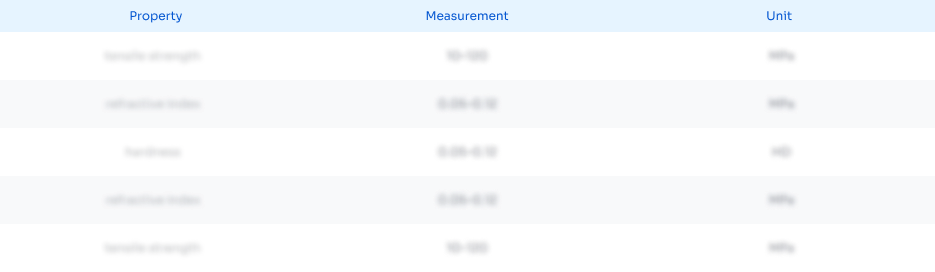
Abstract
Description
Claims
Application Information

- R&D Engineer
- R&D Manager
- IP Professional
- Industry Leading Data Capabilities
- Powerful AI technology
- Patent DNA Extraction
Browse by: Latest US Patents, China's latest patents, Technical Efficacy Thesaurus, Application Domain, Technology Topic, Popular Technical Reports.
© 2024 PatSnap. All rights reserved.Legal|Privacy policy|Modern Slavery Act Transparency Statement|Sitemap|About US| Contact US: help@patsnap.com