Converter pretreatment and cold charging and heating method for high-carbon and high-alloy continuous casting slab
A heating method and continuous casting slab technology, applied in the field of metallurgy, can solve problems such as unreasonable connection of continuous casting slab hot delivery and hot charging process, casting slab fracture, oxidative decarburization of corners, etc., to achieve the suppression of brittle structure and oxidative decarburization The formation of the carbon layer, the change of the organizational form, and the effect of ensuring smooth production
- Summary
- Abstract
- Description
- Claims
- Application Information
AI Technical Summary
Problems solved by technology
Method used
Image
Examples
Embodiment 1
[0051] The billet material is hot-formed steel, and its chemical composition is C: 0.34%, Si: 0.61%, Mn: 1.74%, P: 0.011%, S: 0.002%, Cr: 0.24%, V: 0.155%, Nb : 0.035%, Als: 0.56%; it belongs to the steel type with high carbon content, high manganese content and high vanadium content.
[0052] The thickness of the slab is 230mm. After the continuous casting production, the two slabs off the assembly line are slowly cooled for 75 hours according to the following continuous casting slab stacking and slow cooling method; before hot rolling production, the following continuous casting slab preheating method is preheated for 12 hours , the temperature measured by the temperature measuring gun is 433°C; the hot rolling is heated by a walking beam heating furnace, the temperature in the preheating section of the hot rolling heating furnace is 715°C, and the preheating time is 68 minutes. The time is 63 minutes, the second heating temperature is 1106°C, the soaking temperature is 1244...
example 1
[0056] The billet material is chrome-molybdenum steel for high-pressure gas cylinders, and the chemical composition is C: 0.32%, Si: 0.44%, Mn: 1.54%, P: 0.010%, S: 0.002%, Cr: 1.14%, Mo: 0.260 %, Nb: 0.005%, Als: 0.06%; it belongs to the steel type with high carbon content, high manganese content, high chromium content and high molybdenum content;
[0057] The thickness of the slab is 230mm, 8 slabs are produced by continuous casting, 4 slabs are hot sent and hot loaded and rolled, and the remaining 4 slabs are rolled off the assembly line, and they are conventionally stacked until they are completely cooled. After the remaining slabs were placed for several days, they were ready to be produced again. When the quality of the slabs was checked before furnace loading, it was found that there were a large number of cracks at the corners of the slabs that could not be removed, and production could not continue. The remaining slabs could only be scrapped.
example 2
[0059] The billet material is reinforced plastic high-strength steel, and its chemical composition is C: 0.26%, Si: 0.45%, Mn: 2.03%, P: 0.010%, S: 0.002%, Cr: 0.03%, V: 0.005%, Nb: 0.005%, Als: 0.76%; it belongs to the steel type with high carbon content, high manganese content and high aluminum content;
[0060] The thickness of the slab is 230mm, and the continuous casting produces 8 slabs, which are conventionally stacked until completely cooled. When checking the quality of the slab before charging, no cracks were found, and then the furnace was heated in a conventional way. The temperature requirement of the preheating section is ≤1100°C, the actual temperature of the preheating section is 1053°C, and the preheating time is 32 minutes; the temperature requirement of the first heating section is 1100-1250°C, the actual temperature of the first heating section is 1186°C, and the time is 34 minutes; the second heating section The temperature of the section is 1200-1320°C, ...
PUM
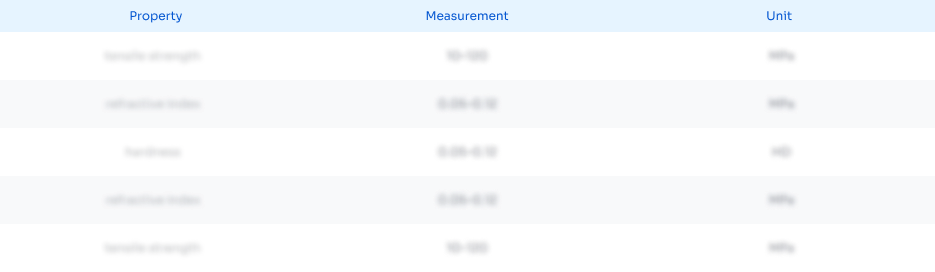
Abstract
Description
Claims
Application Information

- Generate Ideas
- Intellectual Property
- Life Sciences
- Materials
- Tech Scout
- Unparalleled Data Quality
- Higher Quality Content
- 60% Fewer Hallucinations
Browse by: Latest US Patents, China's latest patents, Technical Efficacy Thesaurus, Application Domain, Technology Topic, Popular Technical Reports.
© 2025 PatSnap. All rights reserved.Legal|Privacy policy|Modern Slavery Act Transparency Statement|Sitemap|About US| Contact US: help@patsnap.com