Purification smelting process of wear-resistant castings
A technology of purification and craftsmanship, applied in the field of purification and smelting of anti-wear castings, can solve problems such as unsatisfactory deoxidation effect, low material purity, and affecting high-end products, so as to reduce oxidized inclusions and reduce the probability of reaction , the effect of prolonging the service life
- Summary
- Abstract
- Description
- Claims
- Application Information
AI Technical Summary
Problems solved by technology
Method used
Examples
Embodiment 1
[0039] A purification smelting process for anti-wear castings proposed by the present invention comprises the following steps:
[0040] S1. Select steel scrap, ferrochrome alloy, ferromolybdenum alloy, ferromanganese alloy, ferrosilicon alloy, ferrovanadium alloy, ferrotungsten alloy, ferronickel alloy, ferrohafnium alloy and rare earth ferroalloy as raw materials;
[0041] S2. Put steel scrap into the smelting equipment, melt 1 / 3, add ferrochrome alloy and ferromolybdenum alloy for smelting, then add ferromanganese alloy, ferrosilicon alloy, ferrovanadium alloy, ferrotungsten alloy, ferronickel alloy, ferrohafnium alloy and rare earth iron alloy for smelting, add deoxidizer to purify , Obtain pre-deoxidized molten steel after slag removal;
[0042] S3. Use a diffusion deoxidizer to perform a diffusion deoxidation, then use ferrosilicon and ferromanganese to carry out precipitation deoxidation, then use a diffusion deoxidizer to perform a second diffusion deoxidation, and then...
Embodiment 2
[0046] A purification smelting process for anti-wear castings, comprising the following steps:
[0047]S1. Select steel scrap, ferrochrome alloy, ferromolybdenum alloy, ferromanganese alloy, ferrosilicon alloy, ferrovanadium alloy, ferrotungsten alloy, ferronickel alloy, ferrohafnium alloy and rare earth ferroalloy as raw materials; wherein, the size of each raw material is 40-60mm;
[0048] S2. Put steel scrap into a one-to-two intermediate frequency induction furnace, melt 1 / 2, add ferrochrome alloy and ferromolybdenum alloy for melting, then add ferromanganese alloy, ferrosilicon alloy, ferrovanadium alloy, ferrotungsten alloy, ferronickel alloy, ferrohafnium alloy and ferro-rare alloy for melting, Add deoxidizer to purify and remove slag to obtain pre-deoxidized molten steel; the temperature of the smelting is 1450°C; the temperature of the pre-deoxidized molten steel is 1400°C; the weight of the added deoxidizer is 0.15wt of the weight of the molten steel to be treated %;...
Embodiment 3
[0055] A purification smelting process for anti-wear castings, comprising the following steps:
[0056] S1. Select steel scrap, ferrochrome alloy, ferromolybdenum alloy, ferromanganese alloy, ferrosilicon alloy, ferrovanadium alloy, ferrotungsten alloy, ferronickel alloy, ferrohafnium alloy and rare earth ferroalloy as raw materials; wherein, the size of each raw material is 50-90mm;
[0057] S2. Put steel scrap into a one-to-two intermediate frequency induction furnace, melt 1 / 2, add ferrochrome alloy and ferromolybdenum alloy for melting, then add ferromanganese alloy, ferrosilicon alloy, ferrovanadium alloy, ferrotungsten alloy, ferronickel alloy, ferrohafnium alloy and ferro-rare alloy for melting, Add deoxidizer to purify and remove slag to obtain pre-deoxidized molten steel; wherein, the temperature of the smelting is 1550°C; the temperature of the pre-deoxidized molten steel is 1420°C; The weight is 0.25wt% of the molten steel weight;
[0058] S3. Use a diffusion deoxi...
PUM
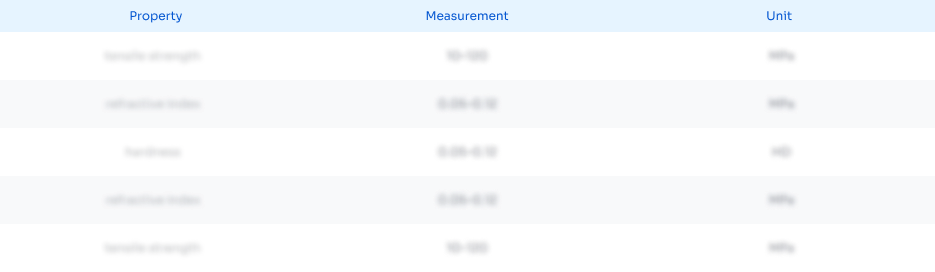
Abstract
Description
Claims
Application Information

- R&D
- Intellectual Property
- Life Sciences
- Materials
- Tech Scout
- Unparalleled Data Quality
- Higher Quality Content
- 60% Fewer Hallucinations
Browse by: Latest US Patents, China's latest patents, Technical Efficacy Thesaurus, Application Domain, Technology Topic, Popular Technical Reports.
© 2025 PatSnap. All rights reserved.Legal|Privacy policy|Modern Slavery Act Transparency Statement|Sitemap|About US| Contact US: help@patsnap.com