High-temperature and high-low cycle composite fatigue test system
A fatigue test and high temperature technology, applied in the direction of using repetitive force/pulse force to test the strength of materials, measuring devices, instruments, etc., can solve the problem that the working environment of aero-engine engineering parts cannot be simulated, the fatigue characteristics of materials cannot be accurately reflected, and the fatigue characteristics of materials cannot be fully satisfied. Test requirements and other issues, to achieve the effect of low cost, simple and practical test system
- Summary
- Abstract
- Description
- Claims
- Application Information
AI Technical Summary
Problems solved by technology
Method used
Image
Examples
Embodiment Construction
[0028] The technical scheme of the present invention will be described in further detail below in conjunction with accompanying drawing and embodiment:
[0029] See attached Figure 2-5 As shown, this kind of high temperature, high and low cycle composite fatigue test system includes a main control computer for receiving and processing data, and also includes a low cycle loading device and a high frequency vibration device, among which:
[0030] The low cycle loading device includes a rigid frame structure arranged on the main platform table 11, the rigid frame structure is a quadrilateral rigid structure composed of load-bearing structure pull rods 9 and load-bearing structure front and rear plates 10, wherein the load-bearing structure pull rods 9 is in the transverse position and parallel to the actuating rod 5 of the low-circumference force hydraulic actuator 4; A hydraulic oil tank 15 and a hydraulic oil pump 14 are installed under the table 11;
[0031] On the frame st...
PUM
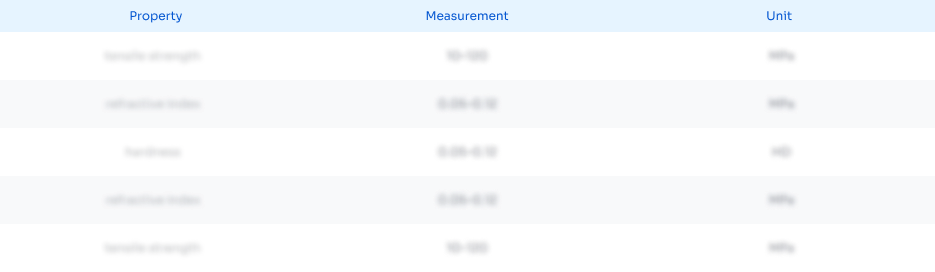
Abstract
Description
Claims
Application Information

- R&D
- Intellectual Property
- Life Sciences
- Materials
- Tech Scout
- Unparalleled Data Quality
- Higher Quality Content
- 60% Fewer Hallucinations
Browse by: Latest US Patents, China's latest patents, Technical Efficacy Thesaurus, Application Domain, Technology Topic, Popular Technical Reports.
© 2025 PatSnap. All rights reserved.Legal|Privacy policy|Modern Slavery Act Transparency Statement|Sitemap|About US| Contact US: help@patsnap.com