Manufacturing method of watertight cable special for deep diving equipment
A technology of watertight cables and manufacturing methods, which is applied in the direction of cable/conductor manufacturing, insulated cables, heat treatment equipment, etc., and can solve the problem of inability to effectively guarantee the safety of personnel and the safe operation of deep-sea ships, watertightness, airtightness and corrosion resistance , poor wear resistance and flame retardancy, poor water pressure resistance and other problems, to achieve the effects of no dripping, no halogen, flame retardant, environmental protection, safe operation, and high watertight performance
- Summary
- Abstract
- Description
- Claims
- Application Information
AI Technical Summary
Problems solved by technology
Method used
Image
Examples
Embodiment Construction
[0053] The technical solutions of the present invention will be clearly and completely described below in conjunction with the embodiments. Apparently, the described embodiments are only some of the embodiments of the present invention, not all of them. Based on the embodiments of the present invention, all other embodiments obtained by persons of ordinary skill in the art without creative efforts fall within the protection scope of the present invention.
[0054] see Figure 1-2 Shown, a kind of manufacturing method of deep diving equipment special watertight cable, the manufacturing method of described watertight cable specifically comprises the following steps:
[0055] Step 1, material selection;
[0056] Step 2, wire drawing: tinned copper single wire made by copper large drawing-middle drawing-small drawing-annealing and tinning;
[0057] Step 3: Conductor layered stranding and gluing: use a special stranding mold to layer the conductors, and use a special device to ap...
PUM
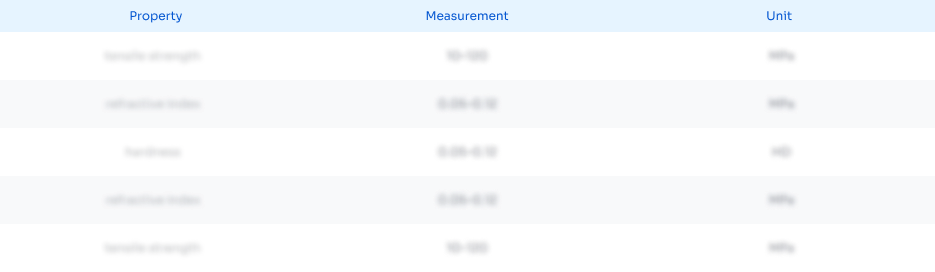
Abstract
Description
Claims
Application Information

- Generate Ideas
- Intellectual Property
- Life Sciences
- Materials
- Tech Scout
- Unparalleled Data Quality
- Higher Quality Content
- 60% Fewer Hallucinations
Browse by: Latest US Patents, China's latest patents, Technical Efficacy Thesaurus, Application Domain, Technology Topic, Popular Technical Reports.
© 2025 PatSnap. All rights reserved.Legal|Privacy policy|Modern Slavery Act Transparency Statement|Sitemap|About US| Contact US: help@patsnap.com