A system and method for automatic roll changing and receiving of flexible coils
A coiled material, automatic technology, applied in the direction of coiling strip material, thin material handling, transportation and packaging, etc., can solve the problems that the production cost cannot be effectively controlled, the production cost cannot be effectively controlled, and the automatic operation is not realized, and the automation is achieved. The effect of high degree, low labor cost and reduction of raw material loss
- Summary
- Abstract
- Description
- Claims
- Application Information
AI Technical Summary
Problems solved by technology
Method used
Image
Examples
Embodiment
[0034] The present embodiment of a flexible coil for automatic coiling and receiving system, e.g., Figure 2 Shown, including the first unwinding mechanism 4, the second unwinding mechanism 5, the first unwinding negative pressure conveying device 6, the second unwinding negative pressure conveying device 7, the main negative pressure conveying device 8 and the gluing device 9, the first unwinding mechanism is provided with a first coil 10, the first coil is released by the first unwinding negative pressure conveying device for transportation and sent to the main negative pressure conveying device, the second unwinding mechanism is provided with a second coil 11, the second coil is released by the second unwinding negative pressure conveying device for transportation and fed into the main negative pressure conveying device On the main negative pressure conveying device, there is a gluing device located between the first unwinding negative pressure conveying device and the second un...
PUM
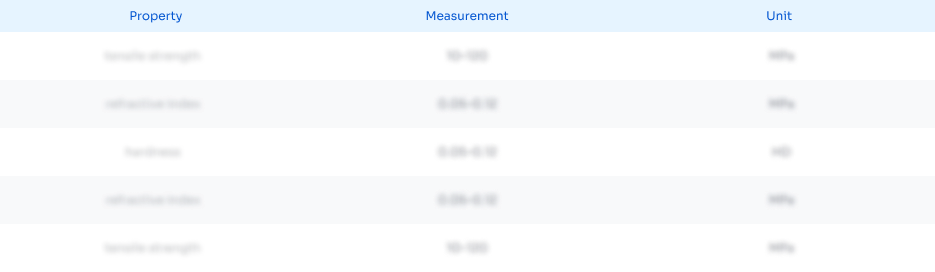
Abstract
Description
Claims
Application Information

- R&D
- Intellectual Property
- Life Sciences
- Materials
- Tech Scout
- Unparalleled Data Quality
- Higher Quality Content
- 60% Fewer Hallucinations
Browse by: Latest US Patents, China's latest patents, Technical Efficacy Thesaurus, Application Domain, Technology Topic, Popular Technical Reports.
© 2025 PatSnap. All rights reserved.Legal|Privacy policy|Modern Slavery Act Transparency Statement|Sitemap|About US| Contact US: help@patsnap.com