Preparation method of laminated porous nitride micro-sheet/S composite positive electrode material
A composite positive electrode material and nitride technology, applied in the field of materials, can solve the problem of low sulfur loading, achieve high sulfur loading, excellent electrochemical performance, and high stacking density
- Summary
- Abstract
- Description
- Claims
- Application Information
AI Technical Summary
Problems solved by technology
Method used
Image
Examples
Embodiment 1
[0031] (1) Preparation of stacked oxides
[0032] Dissolve 0.324g of ammonium metavanadate powder in 30mL of ethanol aqueous solution, wherein the volume ratio of ethanol to water in the ethanol aqueous solution is 1:9, then add dilute hydrochloric acid to the alcohol solution of ammonium metavanadate to adjust the pH value to 2, fully stirred to make it evenly dispersed, poured into the reaction kettle, added iron-cobalt-nickel alloy wire and reacted at 160°C for 4 hours; after the reaction, filtered by suction and dried at 60°C to obtain V 2 o 5 laminated microsheets;
[0033] (2) Preparation of laminated porous nitride
[0034] Will make the V 2 o 5 The laminated microsheets were put into a tube furnace for nitriding, and kept at 600°C for 2h in an ammonia atmosphere. Take it out of the tube furnace when the temperature is lowered to room temperature, and the VN laminated porous material is obtained.
[0035] (3) Preparation of laminated porous nitride / S composites
...
Embodiment 2
[0038] (1) Preparation of stacked oxides
[0039] Dissolve 0.628g of ammonium metavanadate powder in 30mL of ethanol aqueous solution, wherein the volume ratio of ethanol and water in the ethanol aqueous solution is 1:3, then add dilute hydrochloric acid to the alcohol solution of ammonium metavanadate to adjust the pH value to 1, fully stirred to make it evenly dispersed, poured into a reaction kettle, added iron-cobalt-nickel alloy wire and reacted at 180°C for 3 hours; after the reaction, filtered by suction and dried at 60°C to obtain V 2 o 5 laminated microsheets.
[0040] (2) Preparation of laminated porous nitride
[0041] Will make the V 2 o 5 The laminated microsheets were put into a tube furnace for nitriding, and kept at 500°C for 2h in an ammonia atmosphere. Take it out of the tube furnace when the temperature is lowered to room temperature, and then obtain the VN stacked multilayer porous sheet-like structure material.
[0042] (3) Preparation of laminated p...
Embodiment 3
[0045] (1) Preparation of stacked oxides
[0046] First, 0.324g of ammonium metavanadate powder is dissolved in 50mL of ethanol aqueous solution, wherein the volume ratio of ethanol and water in the ethanol aqueous solution is 1:5), then dilute hydrochloric acid is added to the alcohol solution of ammonium metavanadate to adjust When the pH value reaches 4, stir well to make it evenly dispersed, pour it into the reaction kettle, add iron-cobalt-nickel alloy sheet and react at 140°C for 8 hours; after the reaction, filter it with suction and dry it at 60°C to obtain V 2 o 5 laminated microsheets.
[0047] (2) Preparation of laminated porous nitride
[0048] Will make the V 2 o 5 The laminated microsheets were put into a tube furnace for nitriding, and kept at 600 °C for 1 h in an ammonia atmosphere. Take it out of the tube furnace when the temperature is lowered to room temperature, and then obtain the VN stacked multilayer porous sheet-like structure material.
[0049] (...
PUM
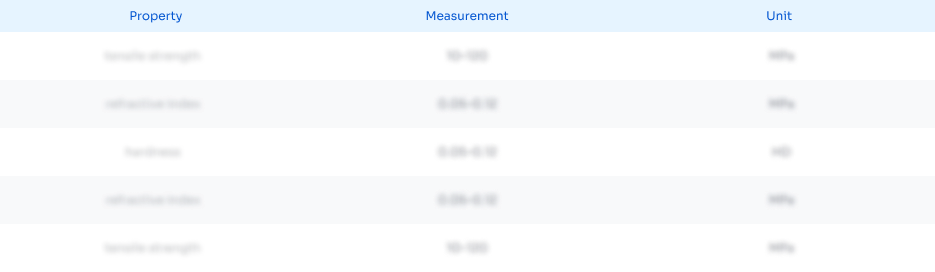
Abstract
Description
Claims
Application Information

- R&D
- Intellectual Property
- Life Sciences
- Materials
- Tech Scout
- Unparalleled Data Quality
- Higher Quality Content
- 60% Fewer Hallucinations
Browse by: Latest US Patents, China's latest patents, Technical Efficacy Thesaurus, Application Domain, Technology Topic, Popular Technical Reports.
© 2025 PatSnap. All rights reserved.Legal|Privacy policy|Modern Slavery Act Transparency Statement|Sitemap|About US| Contact US: help@patsnap.com